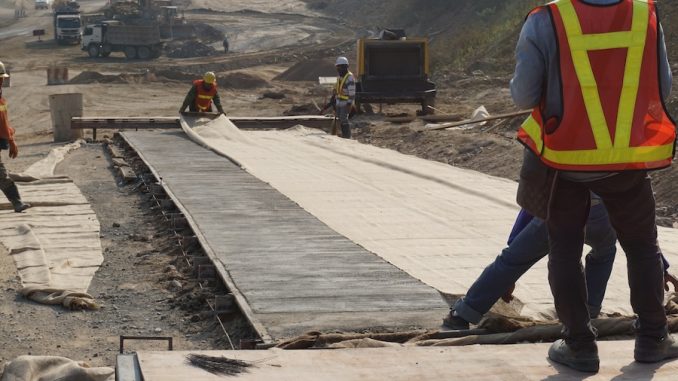
View the complete article here.
Concrete curing is a critical step in the construction process—directly affecting the strength, durability, and longevity of concrete structures. While often overlooked, proper curing ensures that concrete achieves its intended performance by allowing the cement to hydrate properly.
What is Concrete Curing?
Concrete curing is the process of maintaining appropriate moisture and temperature conditions to support the hydration of cement. Hydration is a chemical reaction between water and cement particles, and it is this process that gives concrete its strength and integrity. Curing is essential to prevent the concrete from drying out too quickly—which can cause cracking, shrinkage, and weakness in the structure.
Without adequate curing, the hydration process may stop prematurely—leading to underdeveloped strength and a surface that is more susceptible to damage. The curing process generally spans 7 to 28 days, depending on the project, during which moisture must be maintained for the concrete to fully develop its properties.
The Science Behind Concrete Hydration
When water is mixed with cement, the hydration process begins. This reaction creates calcium silicate hydrate (C-S-H), the primary compound responsible for binding concrete together. Proper curing conditions ensure that the hydration process continues long enough to form a strong and durable matrix. If the concrete dries too quickly or is exposed to extreme temperatures, hydration may be incomplete—resulting in a brittle and porous structure.
Ensuring proper curing enhances concrete’s resistance to external elements—such as freezing and thawing, abrasion, and chemical exposure. It also minimizes the risk of shrinkage cracks that could lead to structural weaknesses down the line.
Common Concrete Curing Methods
Concrete curing plays a pivotal role in ensuring the structural integrity and durability of any project, and choosing the right method is critical to achieving desired results.
Water Curing (Traditional Method)
Water curing, one of the most traditional methods, involves keeping the surface of the concrete wet throughout the curing process. This can be done by continuously sprinkling water, using wet coverings (e.g., burlap or cotton mats)—or creating ponds on the surface.
- Benefits: Maintains constant moisture to facilitate full hydration.
- Challenges: Requires large amounts of water, labor-intensive, and may be impractical in areas with water scarcity.
Membrane Curing
Membrane curing involves creating a barrier on the concrete’s surface to prevent moisture loss. This can be achieved with plastic sheets or by applying liquid membrane-forming compounds.
- Plastic sheets: A cost-effective method that retains moisture by covering the concrete with a polyethylene film.
- Liquid membranes: These are sprayed onto the surface to form a thin, water-retaining layer.
- Pros and cons: Membrane curing is effective in preventing evaporation, but it may not allow excess water to escape—which could lead to surface defects if used improperly.
Steam Curing
Commonly used in precast operations, steam curing accelerates the curing process by applying heat and moisture simultaneously. This method is beneficial for projects requiring early strength development, such as in precast concrete elements.
- Benefits: Ideal for fast-track projects and controlled environments.
- Applications: Precast concrete components, where rapid strength gain is essential.
Curing Compounds
Spray-on curing compounds form a film that seals in moisture. These are particularly useful for large-scale projects where traditional water curing methods may be impractical.
- Advantages: Easy to apply and reduces water needs. Effective for both hot and dry climates.
- Considerations: Care must be taken to ensure proper application, as an uneven coat can result in inconsistent curing.
Modern Technologies in Concrete Curing
Advancements in concrete curing technologies have introduced innovative solutions that improve the efficiency and effectiveness of the curing process.
Internal Curing
Internal curing is an innovative technique where water-absorbing materials, such as lightweight aggregates, are incorporated into the concrete mix. These materials release water slowly, ensuring continuous hydration from within.
- Benefits: Reduces external water needs and helps concrete cure evenly, resulting in fewer cracks and better long-term durability.
- Applications: Especially useful in areas with limited water access or in large-scale structures like bridges and dams.
Sensor Technology for Monitoring Curing
Wireless sensors embedded in the concrete can monitor temperature and humidity in real-time. This data helps contractors optimize the curing process by adjusting environmental conditions as needed.
- Advantages: Provides real-time feedback and allows for precise control over curing conditions, minimizing the risk of under or over-curing.
- Cost implications: While sensors add upfront costs, they can reduce long-term maintenance and repair expenses by improving overall concrete quality.
Self-Curing Concrete
Self-curing, or water-retentive concrete, uses chemical admixtures to retain water during curing. This technology eliminates the need for external curing in some cases, making it ideal for complex projects or where conventional curing methods are challenging.
- Applications: Ideal for remote areas or projects where water access and traditional curing aren’t feasible.
Factors Affecting the Curing Process
Factors that affect the curing process include temperature, humidity levels, and the type of cement and mix design.
Temperature
Concrete curing is highly temperature-sensitive. In hot conditions, concrete may dry too quickly—leading to cracks and reduced strength. Cold conditions slow the hydration process, extending the curing time.
Humidity Levels
Low humidity can cause water to evaporate too quickly, while high humidity may prolong the curing process. Proper moisture levels must be maintained to achieve the desired strength and durability.
Type of Cement and Mix Design
Different cement types and concrete mixes require different curing times and methods. For example, high-performance concrete may need specialized curing techniques to reach its full potential.
Best Practices for Effective Concrete Curing
Consider the following best practices for effective concrete curing…
Timing
Start curing as soon as the surface finishing is completed to prevent premature water loss.
Curing Duration
Typically, curing should last at least 7 days for standard concrete—though 28 days may be required for critical projects or high-performance mixes.
Moisture Management
Ensure adequate moisture throughout the curing period. Use sensors or manual inspections to monitor moisture levels.
Environmental Controls
For large-scale projects, consider using enclosures or windbreaks to protect concrete from environmental extremes during curing.
Conclusion
Concrete curing is a vital process that directly influences the quality and lifespan of any concrete structure. With the variety of curing methods and advanced technologies available today—contractors can ensure that concrete develops the desired strength, durability, and resistance to environmental stresses.
View the complete article here.
What is concrete curing and why is it important?
Concrete curing is the process of maintaining moisture and temperature conditions to support the hydration of cement, which is crucial for the strength and durability of concrete structures. Proper curing prevents issues like cracking, shrinkage, and weakness, ensuring the concrete achieves its intended performance. What are some modern technologies used in concrete curing?
Modern technologies in concrete curing include internal curing, where water-absorbing materials are added to the mix for continuous hydration, and sensor technology, which monitors temperature and humidity in real-time to optimize the curing process. Additionally, self-curing concrete uses chemical admixtures to retain water, eliminating the need for traditional curing methods in some cases.