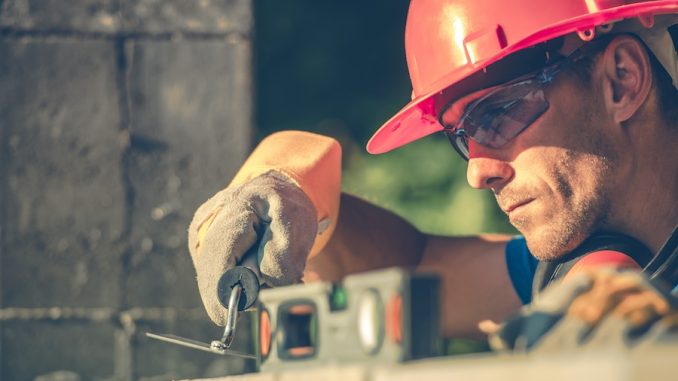
View the complete article here.
Commercial and large-scale masonry projects are a true test of a contractor’s skill, planning, and equipment choices. From massive retaining walls and multi-story commercial facades to complex stone installations, these projects demand precise execution and the right mix of specialized tools. This guide will discuss the essential equipment, strategies for efficient execution, and best practices that will help you excel in these challenging masonry undertakings—ensuring quality and efficiency every time.
Planning and Preparation: Laying the Groundwork for Success
Proper planning is the foundation of any successful commercial or large-scale masonry project. It sets the stage for smooth execution and helps prevent costly delays.
Material Estimates and Logistics
Start by accurately calculating the amount of bricks, blocks, or stone needed for the entire project. Ordering in bulk not only reduces costs but also ensures consistent material quality. However, managing bulk materials requires careful site planning—designate staging areas near the work zone but away from heavy equipment paths to minimize congestion. Utilize bulk material dispensers for easy access to sand and mortar ingredients, speeding up the preparation process.
Site Access and Layout
Large-scale projects often involve heavy machinery like telehandlers and cranes. Assess the site early to identify the best access routes for these machines, and clear any obstacles that may interfere with their operation. Establish efficient flow paths for material movement from delivery points to staging areas to avoid delays. In urban projects, consider compact and maneuverable equipment that can operate in tight spaces.
Weather Considerations
Outdoor masonry projects are subject to changing weather conditions, which can impact both safety and the quality of work. In cold climates, use heated water for mortar mixing and cover exposed sections with insulated blankets to maintain proper curing temperatures. In hot weather, keep materials shaded and pre-soak masonry units to prevent rapid moisture loss—which can weaken mortar bonds.
Essential Equipment for Commercial and Large-Scale Masonry Projects
The right equipment is crucial for tackling the demands of commercial masonry work. Here’s a breakdown of the key tools and machines that make a difference…
High-Capacity Mortar Mixers
Consistency is key when mixing mortar for large-scale projects. Hand-mixing methods are inefficient for high volumes, making industrial-grade mixers like the EZG Mud Hog essential. The Mud Hog handles large batches quickly and consistently, ensuring uniform mortar quality while reducing waste and downtime.
Telehandlers and Cranes
Heavy lifting is a central aspect of commercial masonry. Telehandlers offer flexibility and reach for lifting and positioning bricks, blocks, and stone slabs—while cranes provide the necessary power for handling large precast elements. The use of proper lifting attachments, such as forks and stone clamps, ensures safe and precise material handling.
Grout Delivery Systems
Precision grout placement is vital in structural masonry. Traditional bucket methods are labor-intensive and inefficient. The EZG Grout Hog simplifies the process, providing controlled grout flow and reducing labor costs. It’s particularly useful for multi-story projects, where consistent grout placement is critical for structural integrity.
Cutting and Drilling Tools
Commercial projects often involve dense materials like concrete blocks and natural stone, which require specialized cutting and drilling equipment. Masonry saws with diamond-tipped blades ensure clean, precise cuts—while core drills allow for accurate openings in walls for pipes, conduits, and reinforcements. Water-cooled systems extend blade life and minimize dust for safer operation.
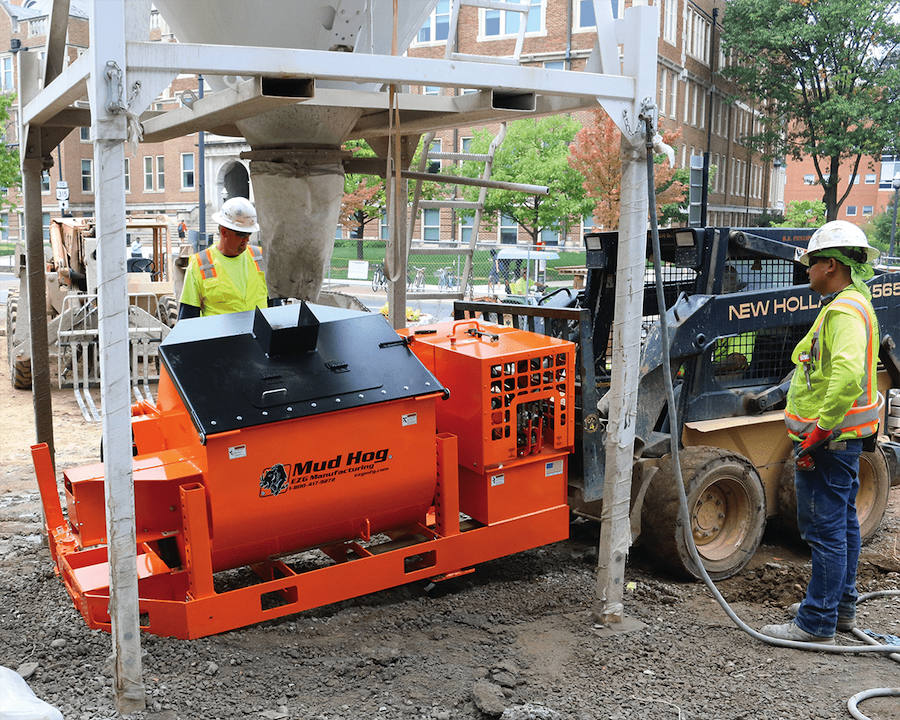
Best Practices for Efficient Large-Scale Masonry Work
Efficiency is key in large-scale projects, where delays can significantly impact budgets and schedules. Here are proven strategies to streamline your workflow…
Optimize Material Staging
Efficient material staging reduces time spent moving supplies. Place pallets of bricks and blocks near the work area, and organize them by size and type for easy access. Utilize bulk dispensers for aggregates and mortar ingredients, and centralize the mixing station to minimize transportation time.
Team Coordination and Role Assignment
Large projects require well-coordinated teams. Assign tasks based on skill level and experience—and ensure clear communication between masons, laborers, and equipment operators. Regular briefings help keep everyone aligned and aware of any changes in the plan, reducing the risk of miscommunication.
Adapting to Weather Conditions
Weather can affect both productivity and the quality of masonry work. In rainy conditions, use tarps to cover materials and avoid working on areas where water could weaken mortar strength. In freezing temperatures, use heaters and insulated blankets to maintain optimal curing conditions. During extreme heat, adjust work hours to cooler parts of the day and keep materials shaded.
Safety Considerations: Protecting Workers and the Job Site
Safety is a top priority in commercial and large-scale masonry projects, where the use of heavy equipment and materials poses significant risks.
Personal Protective Equipment (PPE)
Ensure all workers wear appropriate PPE—including hard hats, eye protection, gloves, and steel-toed boots. When cutting masonry units, use respirators to protect against silica dust—which can cause serious respiratory issues.
Heavy Lifting and Handling
Always follow proper lifting techniques and use the correct tools, such as lifting slings and hooks. Ensure that telehandlers and cranes are operated by certified professionals, and never exceed the load limits of your equipment.
Scaffolding and Fall Protection
Set up scaffolding according to manufacturer specifications and inspect it regularly for stability. Use guardrails, harnesses, and fall arrest systems when working at heights to prevent accidents and injuries.
Pitfalls to Watch Out For (and How to Handle Them)
Even the most experienced contractors can encounter challenges in commercial masonry projects. Recognizing common pitfalls early can help you avoid costly mistakes and delays. Here are some key issues to watch for and tips on how to address them…
Pitfall #1: Inconsistent Mortar Mix Quality
Problem: Inconsistent mortar batches can weaken the structural integrity of the masonry, leading to cracks or uneven bonding. This issue often arises from manual mixing or using low-capacity mixers that cannot handle the volume needed for large-scale projects.
Solution: Invest in a high-capacity, automated mortar mixer—which ensures consistent mixing every time. Train your team on proper mixing techniques and always measure water and ingredients accurately.
Pitfall #2: Poor Material Staging and Logistics
Problem: Inefficient material staging can lead to wasted time, worker fatigue, and increased risk of accidents. This often happens when materials are stored too far from the work area or placed in the path of heavy equipment.
Solution: Plan your material layout carefully at the start of the project. Keep frequently used materials like bricks, blocks, and mortar near the work zone but clear of equipment paths. Use telehandlers and forklifts to efficiently move large quantities of materials as needed.
Pitfall #3: Inadequate Site Preparation
Problem: Failing to properly prepare the site can result in uneven foundations, drainage issues, or structural instability. This is particularly problematic in projects involving retaining walls or multi-story facades.
Solution: Conduct a thorough site assessment before starting work. Address any uneven ground or drainage issues by grading the site and installing proper drainage systems. Use laser levels and other precision tools to ensure a stable foundation.
Pitfall #4: Weather-Related Delays and Quality Issues
Problem: Weather can be unpredictable. Extreme temperatures, rain, or humidity can disrupt the curing process—affecting the strength and durability of the masonry.
Solution: Monitor the weather forecast and be prepared to adjust your schedule accordingly. In cold weather, use heated water in your mortar mix and cover exposed areas with thermal blankets. During hot weather, work during cooler parts of the day and keep materials shaded.
Pitfall #5: Miscommunication Among Team Members
Problem: Poor communication between the project manager, equipment operators, and masonry crew can lead to errors, delays, and even safety incidents.
Solution: Establish clear lines of communication and hold daily briefings to keep everyone informed of the project plan and any changes. Use project management software or communication tools to facilitate real-time updates and coordination.
Final Thoughts
Mastering commercial and large-scale masonry projects requires a blend of skill, strategic planning, and the right equipment. By investing in high-quality tools, following best practices, and embracing new technologies—contractors can deliver exceptional results and tackle even the most demanding projects with confidence.
View the complete article here.
What equipment is essential for large-scale masonry projects?
High-capacity mortar mixers, telehandlers, cranes, grout delivery systems, and cutting tools with diamond-tipped blades are crucial for efficient and high-quality execution. How can contractors minimize weather-related delays in masonry work?
Use heated water and insulated blankets in cold weather, tarps in rainy conditions, and shaded areas during hot weather. Adjust work hours to suit the climate and protect curing masonry from environmental extremes.