
View the complete article here.
A sling—in its most basic definition—is a flexible attachment used between the load and a lifting device. These essential tools are tailored to accommodate loads of various sizes, shapes, and weights, and facilitate their lifting and movement.
The structure of a sling typically comprises the eyes, which are loops at each end of the sling that connect to the lifting device—the body, which bears the weight of the load—and the fittings, which are additional components such as protectors or lifting aids that augment the sling’s lifting capacity or longevity.
Types of Slings
In the diverse landscape of slings, each type is uniquely engineered to meet specific needs and conditions.
Wire Rope Slings
Constructed from steel wires, wire rope slings offer a balance of strength and flexibility. Their high durability makes them ideal for lifting heavy loads—especially in high-temperature environments. However, they are less suited for lifting fragile or irregularly shaped loads due to their rigid structure.
Chain Slings
Made from heavy-duty steel, chain slings are incredibly robust and versatile. They can lift exceptionally heavy loads and withstand harsh environments—including high-temperature settings. They offer excellent flexibility—making them suitable for various lifting operations.
Metal Mesh Slings
These slings combine durability with flexibility. The interconnected metal links conform to the shape of the load, providing a large contact area that reduces load slippage—making them ideal for handling irregularly shaped or unbalanced loads.
Natural or Synthetic Fiber Rope Slings
These slings are soft and flexible, offering gentle contact with the load—which is important when lifting loads with delicate surfaces. However, they’re less durable compared to other types of slings and can be damaged by high temperatures or sharp objects.
Synthetic Web Slings
Crafted from nylon or polyester, synthetic web slings are highly adaptable and lightweight. They offer superior flexibility—making them excellent for lifting awkwardly shaped or delicate loads. However, they can be damaged by high temperatures and some chemicals—limiting their suitability for certain environments.
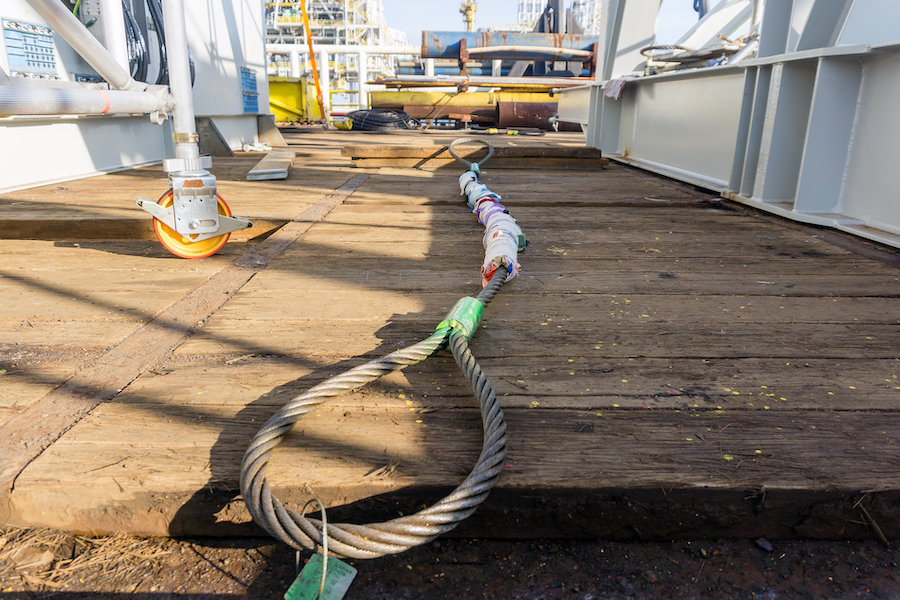
Choosing the Right Sling
The process of selecting the right sling is a crucial aspect of conducting lifting operations safely and efficiently. The right choice isn’t just about securing the load—it’s about protecting workers, maintaining workflow efficiency, and safeguarding the equipment used. That being said, here are general factors to consider for selecting the right sling for the right application…
Load Weight
Every type of sling is designed to handle a specific weight range. Overloading can lead to sling failure—posing a risk to both workers and equipment. For that reason, understanding the weight of the load is the first step in determining the suitable sling type. For example—for heavy loads—one might consider a wire rope sling or a chain sling, both known for their high strength and load capacity.
Load Size and Shape
The dimensions and shape of the load can greatly influence sling selection. Certain types of slings—like chain slings or metal mesh slings—are better suited for irregularly shaped or unbalanced loads, thanks to their flexibility and ability to adapt to the shape of the load. On the other hand, loads with delicate surfaces may be better handled with synthetic web slings or fiber rope slings due to their gentler contact.
Load Temperature
The temperature of the load and the surrounding environment is another factor to consider. If the load or the environment is excessively hot, it may limit the use of slings made from materials that can degrade under high temperatures—such as synthetic web or fiber rope slings. In these types of scenarios, wire rope slings or chain slings—which can withstand high temperatures—may be more suitable.
Lifting Environment
The conditions under which lifting operations are to be performed also play a critical role in the selection of slings. Are operations being conducted indoors or outdoors? Are there any corrosive elements present? Are there sharp edges that could damage the sling? These are all considerations that could affect the selection. For example, an outdoor lifting operation involving sharp-edged loads might call for the use of a wire rope sling with added protective elements.
Nature of the Lift
The type of lift being conducted—whether it’s a vertical lift, a choker lift, or a basket lift—can also influence sling selection. Certain types of slings may be more suitable for specific lift types due to their design and material properties.
The process of selecting the right sling is an exercise in understanding the task at hand, the load characteristics, and the working conditions. An informed choice is crucial to not just the efficiency of the lifting operation, but also the safety of the team and the longevity of the equipment. For that reason, knowing your sling types and their properties is a fundamental aspect of conducting successful lifting operations.
Safety Considerations
When it comes to lifting, prioritizing safety is not just a requirement—but a responsibility that’s key to maintaining a productive and hazard-free workplace. That being said, here are some fundamental safety factors to consider…
Regular Inspections
The first step towards ensuring safety is the implementation of regular, thorough inspections of slings. This process isn’t merely a quick visual check—it’s an in-depth examination of the sling’s structural integrity and performance capability. Inspections should be conducted before each use and also periodically based on the frequency and intensity of use. Trained personnel should assess every element of the sling—links, fibers, wire ropes—for signs of damage or weakness.
Recognizing Signs of Wear-and-Tear
Over time, slings may exhibit signs of wear-and-tear, which—if ignored—can lead to catastrophic failure. These signs could include deformation, such as stretching or twisting—visible damage, like cuts or frayed fibers in synthetic slings or cracks and corrosion in metal slings—or performance issues, like difficulty in handling or loss of flexibility. Early recognition of these signs can allow for timely replacement or repair—maintaining the safety of operations.
Proper Maintenance Practices
In addition to regular inspections, maintenance is a critical practice that can significantly prolong the life of slings. This maintenance includes proper cleaning after use—particularly for slings exposed to corrosive or dirty environments. Dirt and grime can not only degrade the material over time but also obscure visible damage—making inspections less effective. Furthermore, slings should be stored properly when not in use. They should be kept in a dry, well-ventilated area away from direct sunlight, chemicals, or any sharp objects that could cause damage. Metal slings should also be protected against corrosion.
Training
To make all of these practices effective, it’s paramount to invest in training. Team members should be well-trained in the correct use, inspection, and maintenance of slings. They should be able to identify signs of wear and understand the consequences of incorrect usage.
The importance of safety in lifting operations cannot be overstated. By adopting these practices—regular inspections, understanding signs of wear-and-tear, adhering to maintenance procedures, ensuring correct usage, and providing proper training—contractors can ensure that their lifting operations are conducted safely and efficiently—protecting their people, their load, and their productivity.
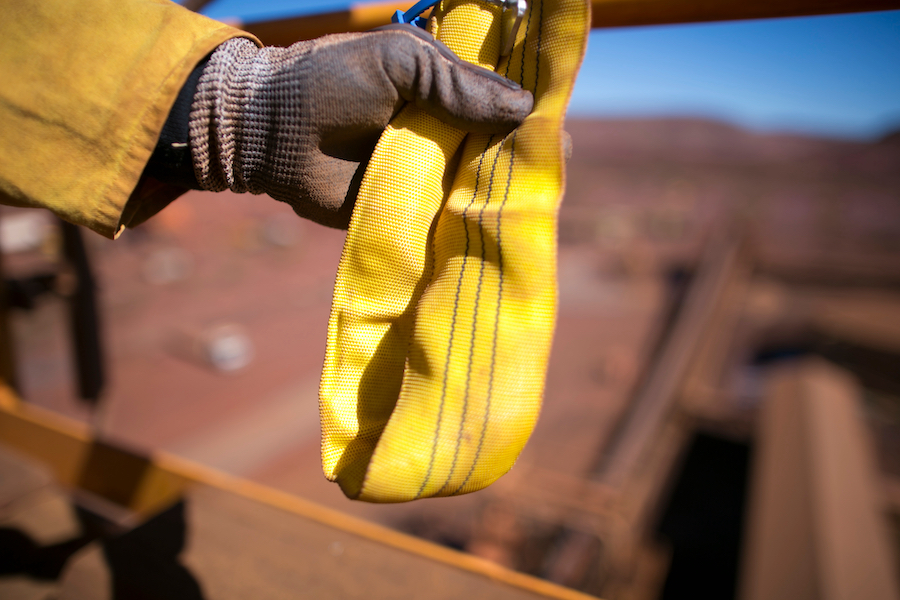
Proper Usage of Slings
Emphasizing proper sling usage is critical not only for maintaining safety on-site but also for ensuring that lifting operations are performed as efficiently as possible. Mastery of sling usage isn’t an inherent skill but an acquired one—necessitating comprehensive training, regular practice, and a thorough understanding of both the principles of lifting and the unique properties of different sling types.
In-Depth Training
At the heart of proper sling usage is in-depth and ongoing training. Training programs should equip operators with the knowledge and skills to handle various types of slings and understand their applications and limitations. From understanding load limits to recognizing potential hazards, training should cover all aspects of sling usage.
Understanding Load Capacities
One of the fundamental aspects of sling usage is respecting the specified load capacities. Overloading a sling not only jeopardizes its integrity but also poses significant safety risks. For that reason, operators must be trained to calculate load weights accurately and select the right sling type and capacity for each lift.
Proper Hitching Techniques
Different lifting scenarios call for different hitching methods—such as vertical, choker, or basket hitches. The choice of hitch significantly influences the stability of the load and the overall safety of the operation. Training should, therefore, cover different hitching techniques—along with their appropriate uses and limitations.
Avoidance of Abrasive Surfaces and Sharp Edges
Improper handling of slings—such as dragging them over abrasive surfaces or loading them over sharp edges—can significantly shorten their lifespan and compromise safety. Workers should be trained to handle slings carefully and use protective measures—like edge protectors or padding—when dealing with sharp-edged loads.
Regular Refresher Courses
Like any skill, the proper usage of slings can weaken over time or become outdated as new technologies and best practices emerge. Regular refresher courses are vital to keep workers’ knowledge and skills up-to-date and reinforce the importance of safe handling practices.
The importance of proper sling usage goes beyond merely lifting and moving loads—it’s a major component of a safe and productive working environment. Through comprehensive training, regular refreshers, and a strong emphasis on safety culture, contractors can ensure that their lifting operations are not only efficient but also reliably safe.
Regulations and Standards
Compliance with industry regulations and standards is not only a legal requirement—it is a fundamental principle that underpins the safety and efficiency of lifting operations. Non-compliance is unacceptable—as it carries not only legal and financial ramifications but also increases the risk of accidents.
To ensure adherence to regulations, regular audits and inspections are crucial. These processes serve as a way to identify any non-compliance and implement necessary corrections promptly. Staying within the guidelines is an ongoing effort that requires vigilance and commitment.
In addition, it’s crucial that everyone involved in lifting operations—from management to ground operators—is aware of these regulations and their significance. This awareness can be facilitated through ongoing training and by cultivating a culture of safety and shared responsibility.
View the complete article here.
What are the main types of slings used in heavy equipment operations?
The main types of slings are wire rope slings, chain slings, metal mesh slings, natural or synthetic fiber rope slings, and synthetic web slings, each designed for specific lifting needs.
How do I choose the right sling for a lifting operation?
Consider factors such as load weight, size, and shape, temperature, lifting environment, and the nature of the lift to choose the appropriate sling type, ensuring safety and efficiency in the lifting process.