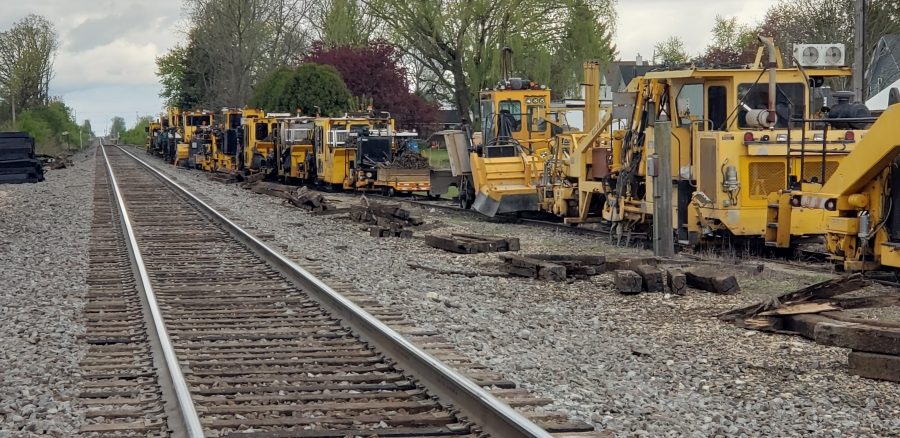
By John Roberts, CEO, Railway Equipment Leasing and Maintenance (RELAM) Inc.
Choosing the right equipment for railway maintenance-of–way (MOW) operations is critical, and so is the decision on whether to lease or buy that equipment. A recent independent analysis performed by a major multinational professional services network quantified the total cost of leasing (TCL) versus the total cost of ownership (TCO) of MoW equipment. The analysis concluded that the factors of greatest impact to the TCL and TCO decision framework center around cost of capital, lease rate, and equipment utilization. As cost of capital increases, lease rate decreases, or equipment utilization decreases, and breakeven points shift more in favor of leasing. Using a leasing model can also help optimize or conserve capital so railroad and contractors can focus on their core business.
Reviewing the factors of interest to Class I railroads, short lines, transits, and contractors
The independent study cited reviewed the lease versus buy decision framework for the key railroad organizational types, which include Class I railroads, short lines, transits, and contractors. The factors considered may affect the organizational types differently.
The framework modeled both tangible and intangible factors. Tangible/quantifiable metrics included purchase price, lease rate, maintenance costs, utilization, cost of capital, useful life, and taxes. Intangibles considered included flexibility, access to new equipment/latest technology, and availability of equipment.
Analysis focused on understanding costs of ownership versus leasing
To understand the cost of ownership versus leasing, one must consider flexibility, utilization, and the cost of capital or covenants in lending.
Critical to the analysis is an evaluation of the customer’s equipment utilization – is the equipment being used frequently, or is the organization tying up its capital for equipment that sits in a maintenance yard and is not used for several months at a time? Many organizations choose not to own a piece of equipment that is sitting idle for large portions of the year when they could instead lease and then return it when they are finished. In addition, if they own equipment, they must store it, maintain it, insure it, and perhaps pay the note in accordance with their credit agreement. Depending upon the part of the country, track maintenance is a seasonal business; they may only get 6-8 months of work time per year in Canada and the northern United States.
Figure 1 illustrates the results of the TCL versus TCO comparison over a 10-year period at various utilization percentages, rental periods, and rental rate factors (monthly lease rate as a percentage of a machine’s original equipment cost). This comparison exercise uses the example of a tamper, an expensive piece of equipment used to pack track ballast under railway tracks to make the tracks more durable. At a cost of more than a million dollars, the tamper has a life of about 8,000 to 13,000 hours (about 1,500 hours are used in a typical year) – which averages to about a 10-year life. This means organizations must make a significant reinvestment in a new tamper every decade should they choose to own it.
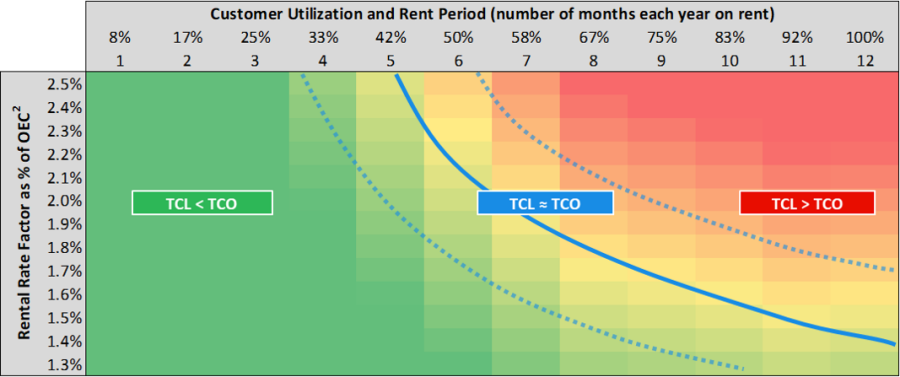
The blue line represents the breakeven point at various lease rate levels (top to bottom) and utilization levels/lease terms (left to right). Dotted lines represent areas of value potentially awarded to intangible considerations. There is a strong argument that leasing late model equipment would be the most efficient option for those with equipment utilization of less than 70 percent, or consistent use for 9+ months of the year.
Digging deeper into the benefits of leasing
Access to new technology
One of the key intangibles that must be considered is the importance of access to new, more efficient technology. This affects various organizational types differently. Benefits of late model fleets such as those offered by Railway Equipment Leasing and Maintenance (RELAM) Inc. may include access to more productive specialized equipment, telematics tools to optimize machines, and more user-friendly and easier to operate equipment that helps with the pressing and ongoing shortage of skilled equipment operators.
Leasing provides organizations with a program in which their fleet is constantly being refreshed. These assets naturally consume themselves, requiring organizations to staff mechanics and carry an inventory of parts – not to mention the pain and suffering that results from an older piece of equipment breaking down in the middle of a job. However, if there is a trade out of equipment every 3-5 years, there are fewer headaches associated with downtime, fewer decreases in customer satisfaction, and fewer increases in costs of maintaining old equipment. With continual access to the latest and greatest equipment and technology, maintenance is carried out more efficiently and more safely.
For example, many transit agencies have narrow clearances, making it difficult for typical maintenance equipment to fit and travel through a tunnel or platform or next to the electric third rail. Transit maintenance departments may use a backhoe, front end loader, or track hoe with attachments to complete work; all of the work gets done, but not in the most efficient manner. Most OEM suppliers do not produce machines that can be used by both Class I and transit railroads, forcing transit agencies to purchase costly special one-off equipment that will not be fully utilized. Many transit projects are short-lived (1-3 years), after which the machines would no longer be needed by the agency unless they are required to perform spot maintenance projects that are subject to planning and budgets.
To meet the current and future needs of both passenger railroads and transit authorities, RELAM is partnering with OEM suppliers to produce pieces of equipment that have been specially adapted to fit their clearances. By expanding its fleet to carry specialized equipment, RELAM is helping transit organizations become more productive.
Reduction of service disruptions due to aging equipment
Another example of the benefits of new technology relates to contractors, who tend to try to age out any equipment they own. This leads to increased repair and maintenance costs, as well as unplanned equipment failures that result in service disruptions and issues with customers. If contractors lease late model equipment instead, they have access to RELAM’s expertise that allows them to optimize use of the equipment and quickly address any problems, should they arise.
In addition, newer machines are equipped with cloud-based telematics tools to optimize the machines and assist with troubleshooting mechanical issues when they arise. Operators get a selection of data that they can use to better manage the operation of their fleet. With configurable telematics, if the machine goes above a certain speed operators receive a text or email alert. Daily reports provide precise information on how many hours the machine worked for the day. Other reports indicate when there is a fault on the machine, and operators can log in and receive a text telling them where the problem resides.
Responding to labor challenges
Challenged with finding skilled maintenance labor and constrained by a shortage of machine operators, railroads and contractors can benefit by leasing late model fleets such as those carried by RELAM. These newer machines are more user-friendly, easier to operate, and require less skill and knowledge than older equipment, helping to augment and address labor challenges and constraints.
Increasing flexibility
In addition to access to new technology, leasing provides increased flexibility. For example, operators can choose a short-term, long-term, or mid-term lease. They can rent equipment for a period of time and then purchase it, continue leasing it, or return it instead of being locked into a 10-15 year commitment on owned equipment.
Also, the piece of equipment an operator purchases today may not be what is needed in the future. Equipment and technology are continually evolving and improving. Leasing equipment helps operators meet not only today’s needs, but also those of tomorrow and beyond. An organization that might need a production tamper for one year might need a chase tamper in the future. These are two very different items and organizations do not want costly equipment sitting idle.
Optimizing limited capital resources
Equipment leasing is also a good solution when capital is limited. This may be a serious issue for those who are looking to obtain funds through the proposed infrastructure bill, which is set to be a catalyst for the U.S. and Canada. Mexico is also pursuing light rail transit projects.
Say, for example, that an organization receives $700 million and wants to accelerate its maintenance initiatives. It could adopt a capital strategy focused on renting-to-own assets. In this way it could leverage dollars out of different budget buckets.
For example, some RELAM leasing customers are following this strategy as a way to create faster change within their organization. Instead of purchasing eight pieces of equipment year-over-year for five years, they buy four direct from the manufacturer and lease four through RELAM. When capital is available, they will purchase the remainder of the equipment, thereby creating velocity within their fleet to create the change they are planning for. In addition, the newer equipment offers a more ergonomic solution for operators.
In addition, most rail organizations seek to optimize or conserve capital as a way of focusing on their core business. By meeting their equipment needs through a leasing model, they can deploy their capital on core competencies, putting it towards growing their business through marketing or sales. Leasing late model equipment is often the most efficient option for those with equipment utilization of less than 70 percent.
Leveraging environmental incentives
Emission reductions is an important trend that RELAM believes will be a focus going forward in society. Most new equipment reduces engine emissions so it can be used for work in California and other states that have, or are contemplating, greenhouse gas (GHG) emissions reductions programs. RELAM’s late model fleet is fully equipped to meet today’s emissions standards.
Leasing model conserves operator capital
Making the right decision on whether to buy or lease equipment for MoW operations is critical to the financial health of all rail operators and contractors. Careful analysis suggests that using a leasing model can be an effective strategy for conserving capital, allowing operators to focus on their core business.