
View the complete article here.
You’ve got expensive equipment that needs to be maintained in order to be ready for the next job, starting with the undercarriage. If your work requires dozers, excavators, or even the tractor trailer to haul it on, you have many moving parts to keep in top condition. Links, pins, bushings, and sprockets are just a few of those basic components, but if any of them fail, you’re done.
What does that mean for you? If your heavy gear fails you, the job won’t get finished and your reputation will pay the price. Worse, as one of the highest operating costs in running your business, the simple truth is you literally can’t afford to have a dozer go down due to the undercarriage. So what are you doing to keep your heavy equipment running smoothly? As it turns out, you might not be doing enough.
No matter what kind of heavy equipment you’re operating, it’s only as good as the undercarriage. Sure, a lot of major components that go into keeping all of the equipment functioning, but that undercarriage has the power to make or break you… maybe even literally.
What Is the Undercarriage?
As the name implies, the undercarriage is the entire framework that’s going to support your heavy equipment. Whether it’s on an earth mover or a 1978 El Camino, that undercarriage is going to do all the heavy lifting (pun intended) when it comes to keeping things moving.
Regardless of the kind of job you take on, operating any track-type vehicle will always mean one thing: a hefty maintenance bill for the undercarriage. In fact, more than half of the upkeep and repair costs you shell out over the lifetime of a single dozer or excavator, for example, will be in seeing to the undercarriage. Factor in the downtime from a job—and even the damage to your company’s reputation when you can’t finish—and the undercarriage starts to look a whole lot more important.
What Do You Need to Know About Your Construction Equipment’s Undercarriage?
It might seem a little strange to put so much emphasis on one part of the entire machine, considering that all the various pieces that make up the undercarriage aren’t all that complicated. But when you put them together and set them in motion, they become a complex piece of finely tuned machinery, and fine tuning means keeping it running the right way to avoid problems.
Unfortunately, there are a lot of things that can lead to undercarriage failure. How you’re using your heavy equipment and where these job sites are located—namely, the type of terrain and weather conditions you’re faced with—can be two of the biggest contributing factors to untimely wear. Nobody wants to say it out loud, but your operators can also be a huge factor in causing your undercarriage to give up on you before it’s time. It’s important that your crew is fully trained and doing things right in order to prevent unnecessary problems. Rushing to get finished can also cause extreme stress on your equipment, so make sure they have enough time to let the vehicle do its job.
Is Your Team Up to the Job?
A note on operators: there are a few major pitfalls that can lead to equipment damage at the hands of an operator, and if you’re on the lookout for them, you can put a stop to them before they become a habit… and an expensive problem. Placing stress on your undercarriage or not making the rear drives do the bulk of the excavation work are two major culprits of operator-caused damage. At the same time, speeding through a job might make your client happy (as long as it’s done right), but your undercarriage components will pay the price by wearing out faster. Make sure your operators are following through with proper work techniques and daily undercarriage inspections.
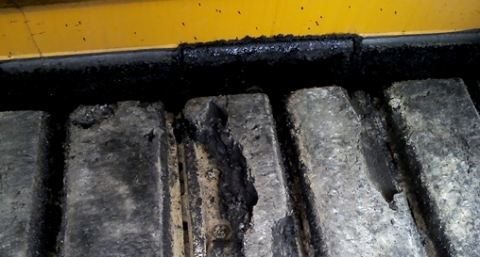
How to Conduct a Simple But Effective Undercarriage Inspection
The simplest way to inspect the undercarriage is just to stand back and look for anything out of the ordinary, so there’s no reason not to do this at the end of every workday. Walk around the equipment itself and give it a very thorough viewing, paying close attention to look for oil spots on the ground. Take a quick look at the spaces in between the pads to make sure there’s no debris caught in there since this can cause extra tension that wears out the pads, shoes, pins, and idlers faster. One obvious sign that there’s something caught may be having less sag in your track than normal, although this is also a sign that your tension could be too tight.
While you’re inspecting the undercarriage, be on the lookout for any loose parts or anything that’s gone missing. This is a good time to get in there and check for uneven teeth wear or cracks. During this daily inspection, pay careful attention to individual components that are showing normal signs of wear but in an uneven way.
Out of Sight, But Not Out of Mind
Just because the undercarriage looks okay, it doesn’t mean you’re done. Inspect the track and track pads, too, and make sure there’s no cracking or uneven wear. If one section of track is wearing its pads more quickly than others, that can be a sign that something’s wrong. There’s no reason to risk an expensive repair and costly delays to your current job due to something as simple as a worn-out track pad or sprocket. If you do see any potential problems, get what you need from a reputable supplier like Everpads and replace the part right away.
Everpads has been in the heavy equipment business since 1995, and undercarriage parts are their specialty. It was built upon one key objective: easily replaceable, bolt-on rubber track pads with proprietary rubber formulas specific to the machinery type. Getting your equipment repaired quickly, effectively, and inexpensively is at the heart of their entire product lineup.
While we’re on the subject of track pads, make sure you’re using the right shoe and size for your particular equipment and the type of job you’re doing; factor in the working conditions (like mud or gravel) and the stress on your equipment.
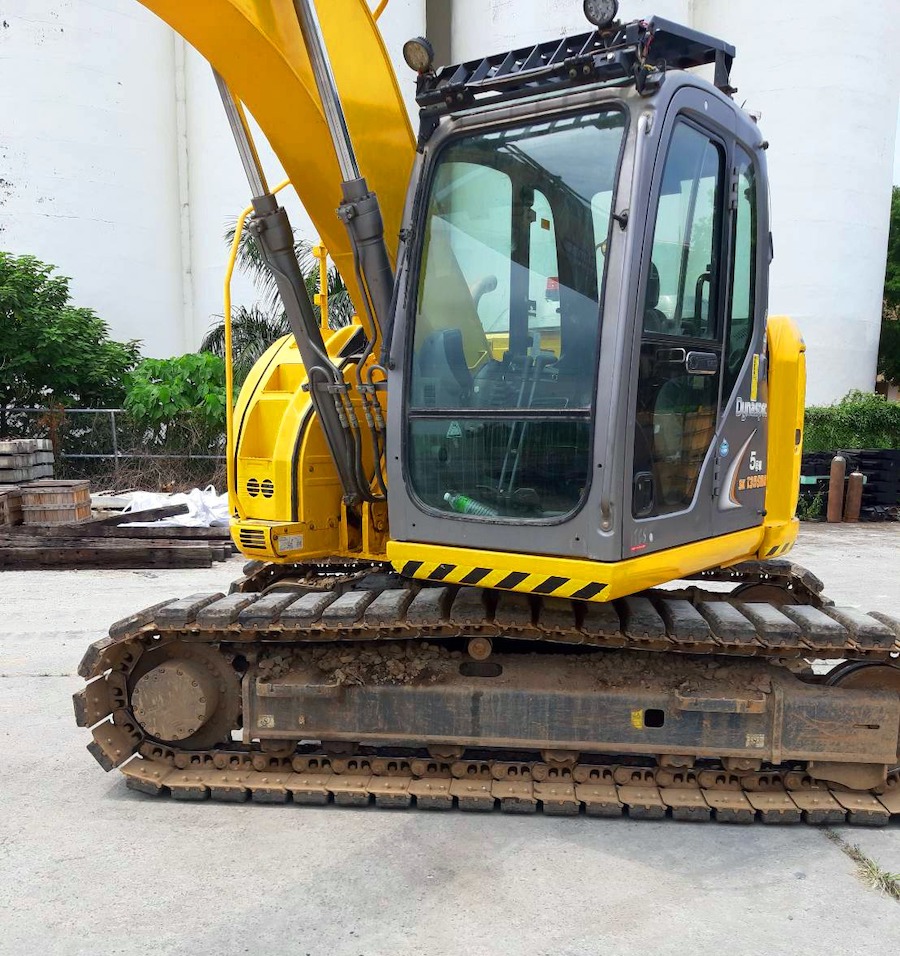
Before You Close Up, You Have to Clean Up
Whether you own, lease, or rent, that machine could cost up to half a million dollars depending on the type. It’s absolutely critical that you clean up the undercarriage and tracks at the end of every single workday. Whether you want to keep your own investment in good working order or you don’t want to be on the hook for damage to a rented or leased machine, it all starts with how you maintain it.
There are a few things you should consider for routine cleanups. At the very minimum, a basic hosing off to loosen any caked-on dirt and mud is a must. A pressure washer or air compressor will do an even better job of eliminating debris at the end of the day, especially from tight spaces. Once it’s clean, grease any components that need good lubricating. Remember, if you don’t have time to clean and grease it right, you don’t have time to take it in for a repair, either.
It All Comes Down to Good Routine Maintenance
The mark of a true professional is someone who takes care of their crew and their gear. The only thing that should be stopping you from getting that next contract is the fact that you already have more work lined up than you can finish. That starts with knowing that your heavy equipment is in the best shape it can be… not sitting in a repair yard somewhere. Take care of your equipment, and it’ll take care of you.
View the complete article here.
Why is the undercarriage maintenance crucial for heavy equipment, and what are the potential consequences of neglecting it?
Proper undercarriage maintenance is vital as it supports the entire framework of heavy equipment, and neglecting it can lead to costly breakdowns, project delays, and damage to a business's reputation.
What are some key tips for conducting an effective undercarriage inspection on construction equipment?
Conducting a daily undercarriage inspection involves visually checking for oil spots, debris between pads, loose or missing parts, and uneven wear; additionally, inspecting tracks, track pads, and cleaning the undercarriage regularly is essential for optimal performance and longevity.