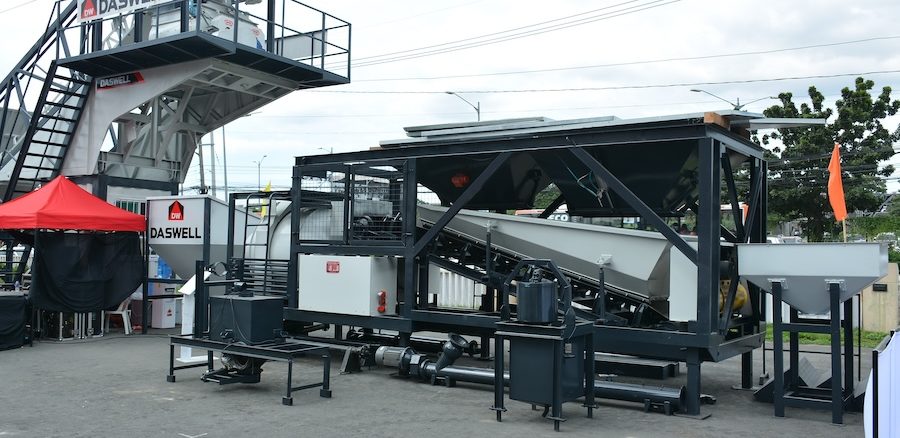
View the complete article here.
This guide provides an in-depth look at the essential stages of setting up and managing a mobile concrete batch plant—covering everything from understanding local regulations and selecting the ideal site to the specific details of plant assembly and daily operations. In addition, we’ll discuss strategies for optimizing production and incorporating environmental considerations to ensure sustainable practices are implemented throughout the process.
Planning and Preparation
Before setting up a mobile concrete batch plant, a comprehensive understanding of local zoning laws and environmental regulations is essential. This section will guide you through the crucial steps of researching and complying with these regulations to ensure your plant operates legally and efficiently.
Understanding Local Regulations
Before setting up a mobile concrete batch plant, it’s crucial to ensure compliance with local zoning laws and environmental regulations. Start by researching the specific requirements of the area where the plant will be located. This research may involve:
- Consulting local authorities: Engage with local zoning boards and environmental agencies to understand all applicable laws and restrictions.
- Securing permits: Identify all necessary permits—which may include land use permits, air and water quality permits, and building permits. The process will likely require detailed documentation and adherence to specific environmental guidelines.
- Planning for inspections: Prepare for mandatory inspections both during and after the setup process. These inspections may focus on safety standards, environmental impact assessments, and operational compliance.
Site Selection
Choosing the right location for a mobile concrete batch plant is paramount to operational efficiency and regulatory compliance. Consider the following criteria when selecting a site:
- Proximity to job sites: Select a site that minimizes transportation distances to major construction sites, reducing transportation costs and material waste.
- Access to roads: Ensure the site is accessible via major roads to facilitate easy and safe transport of materials and equipment.
- Availability of utilities: Check for access to essential utilities, including water supply and electricity. The availability of water is particularly important for concrete production.
- Space and layout: The site should offer enough space not only for the plant itself but also for storage areas for raw materials and finished products. Consider future expansions and ensure the layout allows for efficient workflow and safety compliance.
Acquiring a Mobile Concrete Batch Plant
Selecting the right mobile concrete batch plant involves several factors that influence productivity, efficiency, and overall cost-effectiveness:
- Capacity: Match the plant’s production capacity with your typical project demands. This involves considering the volume of concrete needed on a daily basis.
- Brand and model: Research various manufacturers to find a plant that offers the best balance of quality, service, and price. Look for models that are known for reliability and ease of use.
- Features: Consider the specific features offered by the batch plant—such as automation level, the flexibility of mix designs, and energy efficiency.
- New vs. used: Decide whether to purchase a new or used plant. New plants come with the latest technology and warranties, but used plants can offer significant cost savings. If opting for used, thoroughly inspect the plant for wear and ensure availability of spare parts.
Installation and Setup
The installation and setup of a mobile concrete batch plant are critical stages that determine its operational efficiency and safety.
Transportation and Arrival
Transporting a mobile concrete batch plant requires careful planning to ensure it reaches the site safely and is ready for installation:
- Logistics planning: Coordinate the delivery routes, check for any transportation regulations or road limitations, and prepare for any necessary permits or escorts for oversized loads.
- Site preparation: Before the plant arrives, prepare the installation site by leveling the ground and setting up a stable base. This may involve compacting the soil and adding gravel to ensure a firm foundation that can support the weight of the plant and its operations.
Assembly and Configuration
Setting up a mobile concrete batch plant involves a systematic approach to assembly and utility setup:
- Assembly instructions: Follow the manufacturer’s guidelines for assembling the plant. This includes setting up the main chassis, attaching the mixing tower, and connecting mechanical components like conveyors and bins.
- Utility installations: Ensure the availability of essential services. Connect electrical power to operate the plant machinery, establish a water supply for concrete mixing, and set up any necessary data connections for plant operation controls and monitoring.
Safety Measures
Safety is paramount when operating any heavy machinery, especially a concrete batch plant:
- Safety protocols: Establish safety protocols and emergency procedures. This includes creating clear signage, emergency stop mechanisms, and easily accessible fire extinguishers.
- Staff training: Conduct thorough training for all personnel involved in operating the plant. Focus on the specific operations of the batch plant, the handling of materials, and emergency response actions.
Operational Guidelines
Efficient operation of a mobile concrete batch plant involves meticulous setup and careful daily management. Initial calibration of machinery ensures accuracy, while systematic procedures from startup to shutdown promote safety and efficiency. Proper handling of materials like cement and aggregates prevents contamination, maintaining production quality.
Calibration and Testing
To ensure accurate measurements and consistent product quality, it is essential to calibrate all scales and metering devices before beginning production. This involves adjusting the equipment to match standardized settings and running tests to confirm that readings are correctly aligned with known weights or measures.
Performing a dry run of the machinery is crucial. This process includes testing each component under operational conditions without producing actual product to verify that all parts are working seamlessly together. It helps in identifying any malfunctions or adjustments needed before entering the full production phase.
Daily Operations
Establish clear procedures for both starting up and shutting down the plant each day. This includes checking safety systems, initializing software, and engaging machinery in a set sequence—as well as the reverse process for shutting down, ensuring everything is turned off and secured properly to avoid accidents and equipment wear.
Continuous monitoring of the production process is vital. Regular checks help in spotting any deviations from standard parameters, allowing for immediate adjustments. This might involve tweaking the mix of raw materials, adjusting the speed of conveyors, or recalibrating meters to maintain the desired product quality.
Handling Materials
Proper storage of materials is crucial to maintain their quality and ease of use. Cement should be kept dry and free from contact with moisture, aggregates stored in well-drained areas, water in clean tanks, and admixtures in conditions recommended by their manufacturers. Efficient organization of storage facilities reduces contamination risks and improves accessibility.
To prevent contamination of materials, implement strict control measures such as:
- Using dedicated equipment for different materials to avoid cross-contamination.
- Regular cleaning schedules for all storage and handling equipment.
- Training staff on proper handling techniques to maintain material integrity.
Maintenance and Troubleshooting
Effective maintenance and troubleshooting are fundamental for ensuring the longevity and optimal performance of a mobile concrete batch plant. Regular, structured maintenance schedules help prevent unexpected breakdowns—while accurately diagnosing and resolving common operational issues maintains efficiency and prevents costly repairs.
Regular Maintenance Schedule
Effective maintenance is crucial for the longevity and optimal performance of a mobile concrete batch plant. Implementing a structured maintenance schedule can prevent unexpected breakdowns and ensure operational efficiency.
A maintenance checklist might include:
- Daily: Check lubrication levels, inspect belts and hoses for wear, and ensure that all safety guards are in place.
- Weekly: Test all electrical connections, inspect and clean filters, and check hydraulic systems for leaks.
- Monthly: Conduct thorough inspections of the mixing drum and blades, recalibrate scales and metering devices, and inspect the condition of wear parts.
Also, you should maintain an inventory of essential spare parts based on historical usage data and predicted wear rates. Regularly review and update the inventory to ensure quick replacement of critical components. This practice reduces downtime and increases the reliability of the plant operations.
Troubleshooting Common Issues
When it comes to troubleshooting common operational issues with concrete batch plants, handling the challenges correctly is key to maintaining efficiency. For example—if the concrete mix is inconsistent, it’s essential to check and adjust the calibration of metering devices and to inspect for clogged filters that might be affecting the mix quality. In addition, increased machinery noise or vibration can indicate problems with mechanical components. Inspecting bearings and couplings and replacing worn parts as needed can address these issues.
Deciding whether to handle maintenance issues in-house or seek professional help depends on the complexity of the problem. Basic mechanical issues like replacing filters or adjusting conveyor belts can generally be managed by trained on-site personnel. However—more complex issues, such as electrical faults or software malfunctions, should be addressed by specialized technicians to prevent further damage and ensure that safety standards are maintained.
Efficient Use of a Mobile Batch Plant
To effectively utilize a mobile concrete batch plant, focusing on optimizing production and considering environmental impacts is essential. Employing targeted strategies enhances operational efficiency and meets diverse project requirements, while sustainable practices help minimize ecological footprints—promoting a greener construction process.
Optimizing Production
To maximize the output and efficiency of a mobile concrete batch plant, employing specific techniques and adjusting operations to meet the demands of various projects is essential. Here are some strategies:
- Batch size optimization: Adjust batch sizes based on the demand of the project to minimize waste and increase turnaround time.
- Automated control systems: Use automated control systems for precise material handling, mixture ratios, and batching timings—which help in maintaining consistent quality and reducing human error.
- Regular equipment calibration: Regular calibration of equipment ensures accuracy in material measurement and mix consistency, leading to higher quality output.
- Flexible operation scheduling: Adapt operation schedules based on project deadlines and resource availability to maximize plant utilization without overburdening the machinery.
Environmental Considerations
Implementing sustainable practices within mobile batch plant operations is crucial for minimizing environmental impact and promoting sustainability:
- Use of recycled materials: Incorporate recycled materials like crushed concrete as aggregate in new mixes, which reduces waste and the demand for virgin raw materials.
- Water management systems: Implement systems to recycle water used in the batching process, reducing overall water consumption and minimizing wastewater discharge.
- Energy efficiency: Opt for energy-efficient machinery and solar panels to power plant operations where feasible, reducing the carbon footprint.
- Waste management and recycling protocols: Develop protocols for managing waste materials, such as dust collection systems to gather and reuse dust from concrete batching.
View the complete article here.
What are the key steps for setting up a mobile concrete batch plant?
Key steps include understanding local regulations, selecting an appropriate site, and ensuring proper assembly and utility setup.
How can you optimize the production of a mobile concrete batch plant?
Optimize production by adjusting batch sizes, using automated control systems, and regularly calibrating equipment.