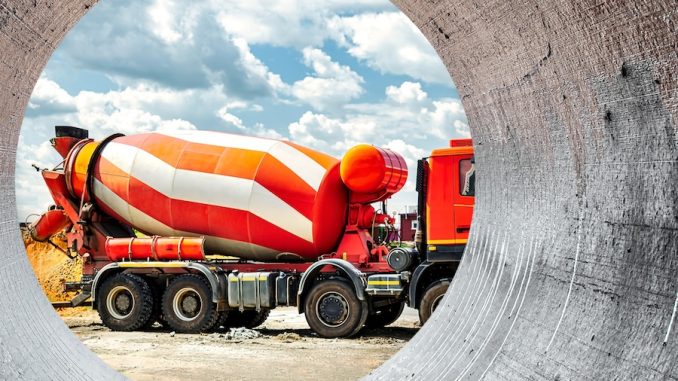
View the complete article here.
Concrete delivery systems are the backbone of the ready-mix industry, enabling the precise production, transportation, and placement of concrete for projects ranging from residential foundations to sprawling infrastructure developments.
Selecting the Right Concrete Delivery Systems
Choosing the appropriate equipment for concrete delivery is a strategic decision that impacts efficiency, scalability, and client satisfaction. Each system must be tailored to project types, volume requirements, and operational constraints.
Batch plants for high-volume production include…
Central-mix plants, like the Vince Hagan HT-12400C ($500,000–$2 million), blend cement, aggregates, water, and admixtures on-site for superior consistency, producing 100–300 cubic yards per hour. These are ideal for high-volume projects such as highways, commercial slabs, or large foundations, where uniform mix quality is critical for structural integrity.
Dry-batch plants, costing $300,000–$1 million, load dry ingredients into mixer trucks for mixing during transit, offering flexibility for smaller or remote operations. With production rates of 50–150 cubic yards per hour, they suit residential developments or mid-sized commercial jobs, balancing cost and output.
Portable batch plants provide mobility for multi-site or rural projects, with setup times of 4–8 hours. Priced at $200,000–$500,000, they deliver 50–100 cubic yards per hour, enabling contractors to serve diverse markets without investing in multiple fixed plants.
For on-site production, consider the following mixers…
For smaller or specialized projects, portable mixers like the EZG Manufacturing Mud Hog® offer a compact, job-site solution for mixing concrete, mortar, or grout. With capacities of 4–20 cubic feet and hydraulic-powered operation, these mixers, priced at $5,000–$15,000, ensure uniform mixes for masonry, precast, or fencing applications. Their portability allows contractors to bypass centralized batch plants for low-volume pours, reducing transportation costs by 10–20%.
Volumetric mixers, costing $200,000–$350,000, produce concrete on-demand at the job site, with adjustable mix designs for precise volumes. Capable of delivering 60 cubic yards per hour, they minimize waste by 15–25% on custom pours, such as residential footings or decorative concrete, making them ideal for urban or remote sites.
Stationary mixers, integrated into batch plants or standalone units ($50,000–$150,000), support high-throughput mixing for precast or specialty applications, ensuring consistent slump and strength for demanding specifications.
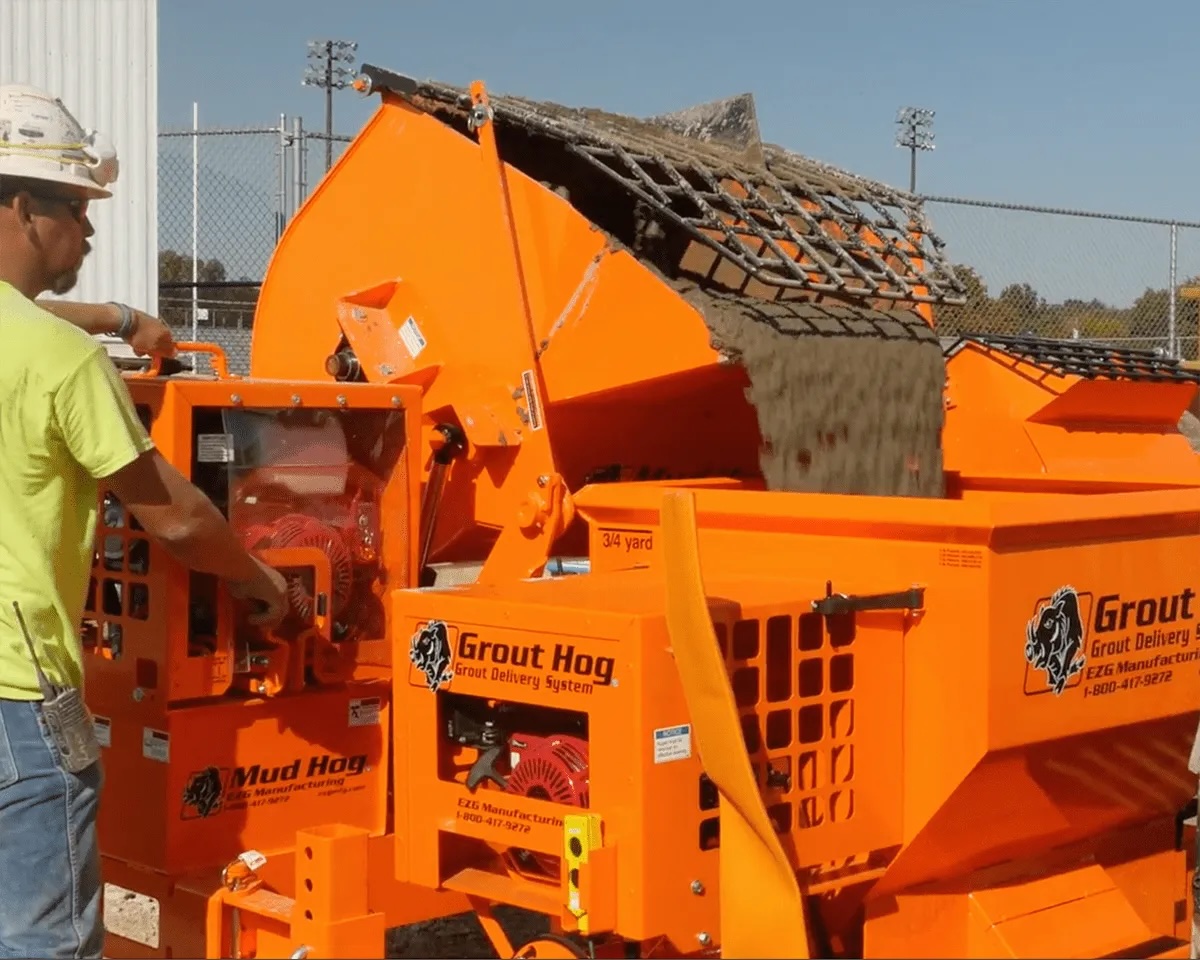
Regarding mixer trucks for transportation, consider the following…
Rear-discharge mixer trucks, such as Mack Granite or Kenworth T880 ($150,000–$250,000), carry 8–12 cubic yards of concrete, with rotating drums maintaining mix homogeneity over 90-minute hauls. Automated water systems allow drivers to adjust slump on-site, ensuring compliance with ASTM C94 standards for workability.
Front-discharge trucks, priced at $160,000–$270,000, offer superior maneuverability on tight job sites, enabling direct placement without additional equipment. Their 8–10 cubic yard capacity suits urban projects like high-rise foundations, where access is limited and speed is critical.
Specialty trucks, like lightweight mixers ($180,000–$300,000), carry 6–8 cubic yards for weight-restricted sites, such as bridges or elevated structures, reducing road wear and ensuring compliance with local regulations.
Pumps and delivery systems for placement include…
Boom pumps, like Schwing SP 1000 ($100,000–$300,000), deliver concrete to elevated or obstructed areas, with a reach of up to 100 feet and pumping rates of 50–100 cubic yards per hour. They accelerate pours for high-rise buildings or bridge decks, cutting placement time by 30–50%.
Line pumps, costing $50,000–$150,000, handle smaller jobs like residential slabs or footings, pumping 20–50 cubic yards per hour. Their compact footprint and 15–30-minute setup time make them ideal for confined spaces, reducing labor costs by 10–20%.
Specialized delivery systems, such as the EZG Manufacturing Precast Hog®, streamline concrete placement for precast projects. Capable of delivering 3 cubic yards in 2.5 minutes with adjustable augers, this system, priced at $20,000–$50,000, enhances precision and reduces vibrating time by 15–25%, making it a valuable tool for precast contractors. Similarly, the EZG Hog Pump® offers towable pumping for grout and concrete, with capacities up to 8 cubic feet, supporting masonry and low-volume pours with wireless remote operation.
Operating Delivery Systems Efficiently
Effective operation of concrete delivery systems requires precision in production, transportation, and placement to meet tight schedules and quality standards. Optimized workflows minimize delays and ensure client satisfaction.
Working with batch plant operations, the following should be considered…
Calibrate plants to produce concrete within ±2% of design mix ratios, using automated controls like CON-E-CO’s PLC systems. Inaccurate batching wastes $50–$100 per cubic yard or risks rejection, costing $5,000–$20,000 per pour. Daily scale checks ensure consistent output.
Optimize production cycles to match delivery schedules. For example, a 100-cubic-yard pour requires 10–12 truckloads over 2–3 hours, demanding 50–60 cubic yards per hour from the plant. Staggered batching prevents truck queues, saving $500–$2,000 in idle time.
Monitor environmental factors, as temperatures above 90°F or below 40°F affect setting times. Use hot water or chillers ($10,000–$50,000) to maintain mix temperatures, reducing defects like cracking by 20–30%.
The following should be considered while working with mixer truck logistics…
Maintain drum rotation at 2–8 RPM during transit to prevent segregation, ensuring uniformity. Deliver within 90 minutes of batching to preserve workability, as delayed concrete requires additives or disposal, costing $500–$1,000 per load.
Plan routes using GPS tools like Telematics to avoid traffic, saving 10–20 minutes per trip and $1,000–$5,000 monthly in fuel and labor. Coordinate with site managers to ensure access, as delays at congested sites can halt pours, costing $2,000–$10,000.
Adjust slump on-site using water or admixtures, but limit additions to 1 gallon per cubic yard to avoid weakening the mix. Train drivers to test slump (3–6 inches for most mixes) with cones, ensuring compliance without stopping pours.
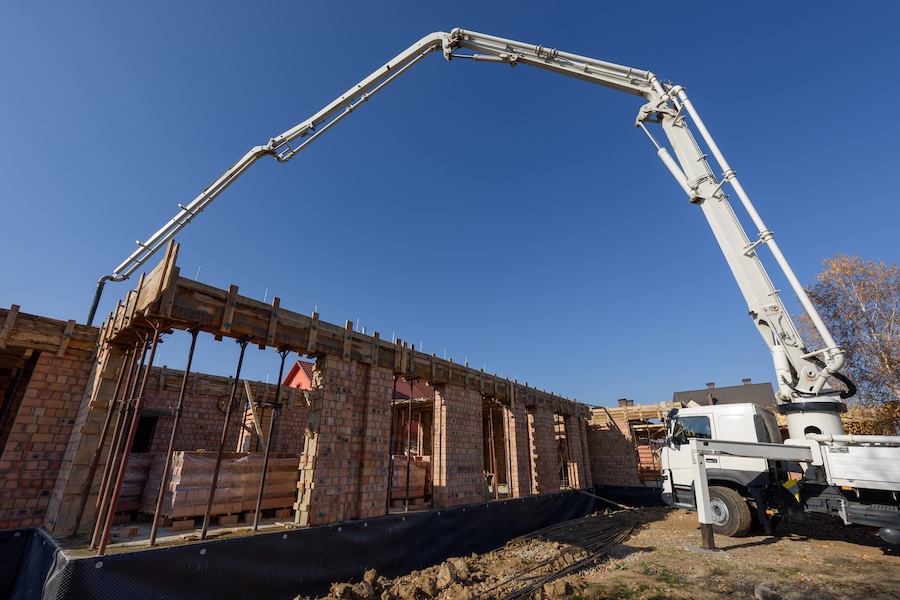
When it comes to pump and conveyor placement, consider the following…
Set up boom pumps with outriggers on stable ground, taking 30–60 minutes, to reach elevated areas safely. Improper setup risks tip-overs, costing $50,000–$100,000 in damages. Use line pumps for smaller jobs, requiring 15–30 minutes to deploy.
Operate conveyors at 100–200 cubic yards per hour for large slabs, adjusting belt speed to match pour rate. Overloading causes spills, wasting $200–$500 per incident. Train operators to monitor belt tension and alignment, preventing jams that delay pours by 1–2 hours.
Coordinate pump and conveyor use with truck arrivals to maintain continuous flow. For a 200-cubic-yard pour, synchronize 20 truckloads with a boom pump’s 80-yard-per-hour capacity, completing the job in 2.5 hours and saving $1,000–$3,000 in labor.
Quality assurance is crucial so be sure to consider…
Test concrete on-site for slump, air content (4–8% for freeze-thaw resistance), and temperature, using portable kits ($500–$2,000). Non-compliant mixes halt pours, costing $5,000–$20,000 in rework or penalties.
Document batch tickets and test results for each load, ensuring traceability. Digital systems like ConcreteDirect automate record-keeping, reducing errors by 15–20% and protecting against liability claims.
View the complete article here.
What type of concrete delivery system is best for high-volume projects?
Central-mix batch plants are ideal for high-volume projects due to their high output (100–300 cubic yards/hour) and superior mix consistency.
How long can concrete stay in a mixer truck before it must be poured?
Concrete should be delivered and poured within 90 minutes of batching to maintain its workability and quality.