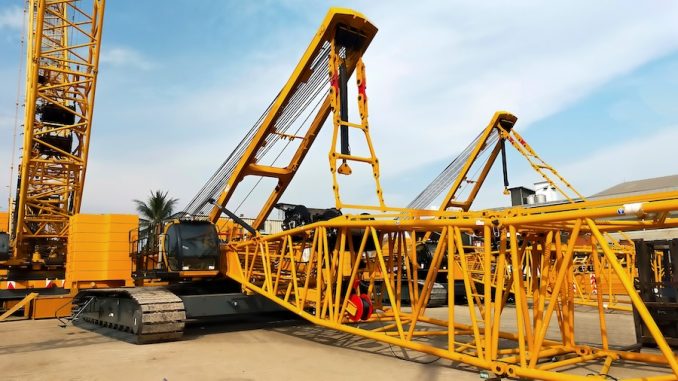
View the complete article here.
Cranes are essential to many industries, from construction to shipping, where lifting heavy loads with precision is critical to the success of a project. However, one of the most significant issues contractors face is crane downtime—which can slow project schedules, increase costs, and negatively impact overall productivity. In this guide, we will explore practical strategies for maximizing crane efficiency and reducing downtime—helping contractors keep their operations running smoothly and on schedule.
Common Causes of Crane Downtime
Before we can effectively reduce downtime, it’s important to understand the main causes. Knowing these can help contractors take proactive steps to prevent problems before they occur.
Mechanical Failures
Mechanical issues—such as worn-out parts, motor malfunctions, or hydraulic system failures—are among the most common reasons for crane downtime. These failures can often be traced back to a lack of preventive maintenance or the use of outdated equipment.
Improper Use
Crane operators who mishandle loads, exceed lifting capacities, or run the crane without breaks may inadvertently cause premature wear-and-tear on equipment. This can lead to mechanical failures that shut down operations.
Lack of Preventive Maintenance
Routine maintenance is essential to keeping cranes in optimal working condition. Failing to regularly check components like wires, cables, and brakes can result in unexpected breakdowns that bring projects to a halt.
Weather Conditions
Extreme weather conditions—such as high winds, rain, or icy environments—can force crane operations to pause. While this type of downtime can’t always be avoided, there are steps contractors can take to minimize its impact.
Operator Errors
Untrained or inexperienced operators are more likely to make mistakes that lead to downtime, whether it’s by mishandling equipment or making poor judgment calls during lifting operations.
Preventive Maintenance Strategies
Preventive maintenance is one of the most effective ways to reduce crane downtime. A well-maintained crane is far less likely to break down, ensuring that projects stay on track.
Scheduled Inspections
Contractors should schedule routine inspections to catch small issues before they become big problems. Inspections should include checking key components such as cables, gears, hooks, and hydraulic systems. Addressing wear-and-tear early can prevent costly repairs down the line.
Lubrication and Fluid Checks
Hydraulic systems are vital to the smooth operation of most cranes, and they require regular monitoring. Make sure to check and maintain proper fluid levels and ensure that parts such as gears, bearings, and wire ropes are adequately lubricated to avoid friction damage.
Part Replacement Timelines
Every crane has components with limited lifespans. Knowing when to replace critical parts like wire ropes, hooks, and brake pads can prevent unexpected breakdowns. Adhering to manufacturer-recommended replacement schedules ensures that cranes are always in top shape.
Software Updates
For cranes equipped with digital systems or automation features, software updates are essential. Keeping control systems up to date ensures compatibility with the latest technology and can help prevent glitches that could result in downtime.
Operator Training and Best Practices
An efficient crane is only as good as its operator. Proper training is crucial to ensure that cranes are used safely and efficiently, minimizing the risk of errors that lead to downtime.
Regular Skill Assessments
Operators should undergo regular assessments to ensure they are up to date on the latest safety standards and best practices. This helps reduce the likelihood of accidents or equipment mishandling.
Load Handling Techniques
Operators need to be well-versed in proper load handling techniques, such as lifting within weight limits and ensuring even distribution. This reduces unnecessary strain on the crane’s components, minimizing wear-and-tear.
Communication and Coordination
Clear communication between the crane operator and the ground crew is essential. Miscommunication can lead to improper load movements or hazardous situations, both of which can contribute to downtime.
Investing in Technology for Efficiency
New technology can play a vital role in improving crane efficiency—providing tools that predict maintenance needs, enhance performance, and minimize human error.
Remote Monitoring Systems
IoT-enabled sensors allow contractors to monitor crane performance in real time. These sensors track the crane’s vital stats, alerting operators and maintenance teams to potential issues before they cause a shutdown. Real-time data collection can also help predict maintenance needs, allowing for more efficient scheduling.
Automation and Smart Cranes
Automation is revolutionizing crane operations. Automated systems can handle certain repetitive tasks with greater precision and consistency, reducing the risk of operator errors. Additionally, smart cranes equipped with advanced safety features can optimize load handling and alert operators to unsafe conditions before they become problematic.
Predictive Maintenance Tools
By leveraging AI and machine learning, predictive maintenance tools can analyze data collected from cranes to forecast when maintenance will be required. This proactive approach prevents unscheduled downtime by allowing contractors to address potential issues ahead of time.
Creating a Downtime Response Plan
Even with the best strategies in place, unexpected downtime can still occur. Having a solid downtime response plan can minimize the impact on your project schedule.
Quick Repair Protocols
Establishing an efficient repair and maintenance team that can quickly respond to issues will drastically reduce the amount of time your crane is offline. Contractors should also ensure that repair teams are trained to handle both minor and major repairs.
Spare Parts Inventory
Keeping a stock of critical spare parts ensures that repairs can be made without waiting for parts to be delivered. This reduces repair times and helps cranes get back in operation faster.
Backup Equipment Solutions
In the event of prolonged downtime—having alternative lifting equipment, such as mobile cranes or smaller hoists, can keep the project moving while the primary crane is being repaired.
Conclusion
Maximizing crane efficiency and reducing downtime requires a proactive approach. By implementing preventive maintenance strategies, investing in operator training, adopting new technology, and establishing a solid downtime response plan, contractors can ensure their crane operations remain smooth and reliable.
View the complete article here.
What are the main causes of crane downtime?
Mechanical failures, improper use, lack of maintenance, weather conditions, and operator errors are common causes of crane downtime. How can contractors minimize crane downtime?
Contractors can reduce downtime by scheduling preventive maintenance, ensuring operator training, adopting advanced technology, and having a downtime response plan.