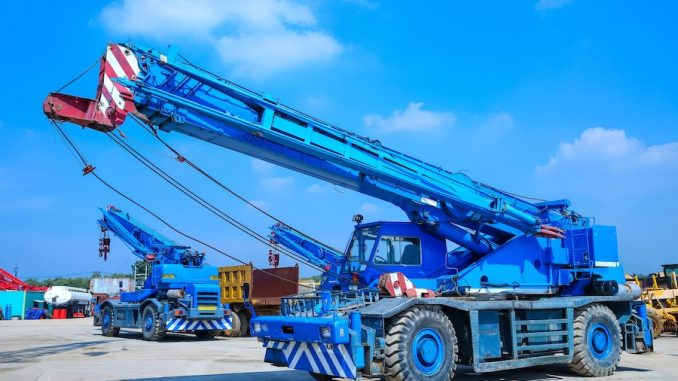
View the complete article here.
Rough terrain cranes have emerged as an indispensable asset for contractors facing challenging projects in demanding environments. In this guide, we discuss the world of rough terrain cranes—exploring their capabilities, key features, best practices, and strategies to tackle the most challenging projects safely and efficiently.
Understanding Rough Terrain Cranes
Rough terrain cranes are purpose-built for navigating uneven, unpaved, and sometimes unstable surfaces where traditional truck-mounted cranes might struggle. Their unique design features include:
- Four-wheel drive capability: Designed to tackle gravel, mud, and rocky surfaces—these cranes use advanced four-wheel drive systems to provide the necessary traction and stability. This is especially crucial on construction sites where the terrain may be unpredictable.
- Articulating booms: These cranes feature booms that can extend and retract, as well as articulate at multiple points. This flexibility allows operators to position loads precisely, even in complex environments with obstacles or confined spaces.
- Compact frame: Many rough terrain cranes boast a compact design, which is ideal for projects with limited access or when working in urban areas. This design aids in maneuverability without sacrificing lifting capacity.
- Off-road tires and suspension systems: Heavy-duty, all-terrain tires coupled with advanced suspension systems enable these cranes to maintain balance and performance over uneven ground—reducing the risk of slippage and equipment instability.
Rough terrain cranes are versatile tools that see use in a variety of challenging environments, including:
- Construction sites: They excel on sites with variable ground conditions—be it a newly broken surface or a site with old, uneven paving. Their adaptability makes them a go-to choice for large-scale building projects.
- Industrial projects: From power plants to refineries, these cranes are essential for lifting heavy equipment and materials in environments where the ground may not be perfectly level or stable.
- Infrastructure developments: Projects such as bridge construction, roadway expansion, and foundation work benefit from the mobility and precision offered by rough terrain cranes—ensuring safe and efficient material handling.
- Remote or disaster-affected areas: When conventional equipment cannot reach remote or damaged sites, rough terrain cranes become invaluable. Their off-road capabilities allow them to operate where other machinery might be immobilized.
Key Features and Technical Specifications
Rough terrain cranes offer a wide range of lifting capacities—from 20 tons up to 100+ tons. This flexibility means that contractors can select a crane that meets the specific needs of each project—whether it involves lifting heavy industrial machinery or delicate, precision components.
Modern cranes come with various boom options, including telescopic and lattice booms. Telescopic booms provide smooth extension and retraction, making them ideal for jobs that require variable reach. Lattice booms offer superior strength and stability for heavy loads at extended lengths.
Additionally, some models include variable geometry features that let operators adjust the boom configuration on the fly—enhancing operational flexibility.
Stability is paramount when lifting heavy loads on uneven terrain. Outriggers are extended to create a broader base of support, while counterweights are meticulously calculated to balance the load. When working on softer surfaces, outrigger pads distribute the weight more evenly—minimizing the risk of ground penetration or slippage. Operators rely on comprehensive load charts and increasingly sophisticated digital stabilization systems that help calculate safe operating limits in real time.
Despite their robust construction, many rough terrain cranes are designed for quick setup and disassembly. This mobility is a boon for contractors who need to move equipment rapidly between multiple job sites.
Modern cranes feature ergonomic cabins equipped with digital displays, advanced sensor integration, and intuitive control systems. These upgrades not only improve precision but also enhance overall operator comfort and safety.
Some models offer remote monitoring capabilities that provide real-time feedback on load status, boom angle, and overall stability—allowing for more precise operations.
Best Practices for Operating Rough Terrain Cranes
Successful crane operations begin with meticulous planning.
Conduct thorough surveys of the operational area. Assess ground conditions, identify potential obstacles, and determine the best access routes. Utilize GPS mapping and drone surveys to create detailed site models, ensuring that every potential hazard is accounted for.
Load analysis is crucial—including a detailed understanding of the load’s weight, center of gravity, and dimensions. Use advanced simulation tools to model the lift and identify any potential issues before the operation begins. This proactive approach minimizes the risk of unexpected challenges during the lift.
Weather can significantly impact crane performance. High winds, rain, or extreme temperatures require careful scheduling and additional safety measures. Weather monitoring systems to receive real-time updates, allowing for quick adjustments in operational plans.
Maintaining safety is a non-negotiable aspect of crane operations, particularly with the certification and training of operators. Ensure that operators are not only certified but also experienced in handling rough terrain conditions. Continuous training programs help operators stay current with the latest techniques and safety standards.
Routine inspections of tires, hydraulic systems, and mechanical components are critical for preventing equipment failures. Implement structured maintenance schedules that use checklists and digital maintenance logs to track equipment condition and service history.
Use reliable communication tools—such as two-way radios and site-wide alert systems—to ensure that the crane operator, riggers, and ground personnel are always in sync. On larger sites, setting up a centralized command center can facilitate real-time coordination—ensuring that everyone is aware of the operational status.
Develop and rehearse emergency procedures, including shutdown protocols and evacuation plans. Regularly conduct emergency drills to ensure that every team member is prepared for unforeseen events.
Executing a lift with precision and safety requires adherence to on-site best practices.
Always deploy outriggers on firm ground. In situations where the ground is too soft, use mats or cribbing to distribute the load evenly. Be prepared to adjust the positioning of outriggers based on real-time ground feedback.
Employ spotters or advanced monitoring systems to track the load’s movement continuously. This ongoing assessment helps identify any deviations from the planned path early.
Maintain a constant line of communication between the operator, riggers, and site supervisors. Establish regular check-ins throughout the operation to confirm that all team members are aligned and that any potential issues are addressed immediately.
Overcoming Challenges in Difficult Projects
Rough terrain projects often come with unpredictable ground conditions.
Select cranes that feature adjustable outrigger systems and other adaptive features to cope with variable terrain. Utilize geotextile fabrics, gravel mats, or temporary concrete pads to stabilize particularly problematic areas.
For areas with loose or shifting soil, pre-lift stabilization can be crucial. Consider consulting with geotechnical experts to implement tailored stabilization strategies that ensure safe crane operations.
Many projects require lifting in environments where space is limited.
Choose the right model, opting for cranes with a smaller footprint that do not compromise on lifting capacity. These models are not only easier to maneuver in confined spaces but also allow for more precise load placement.
Modern cranes are equipped with advanced control systems that facilitate fine-tuned movements. Utilizing remote control options can help operators perform delicate lifts, especially when navigating around obstacles or within crowded workspaces.
Environmental challenges can add layers of complexity to lifting operations.
Some cranes now include integrated wind sensors and environmental monitors that adjust operational parameters automatically during adverse weather.
In urban or environmentally sensitive areas, the noise and emissions from heavy equipment can be a significant concern. Consider models designed with noise reduction technologies and lower emissions, which can help in meeting stringent local regulations while minimizing the environmental impact.
View the complete article here.
What are rough terrain cranes used for?
Rough terrain cranes are used for lifting heavy loads in uneven, off-road, or hard-to-access environments like construction sites and disaster zones.
How do rough terrain cranes stay stable on uneven ground?
They use outriggers, counterweights, and digital stabilization systems to maintain balance and safety on rough surfaces.