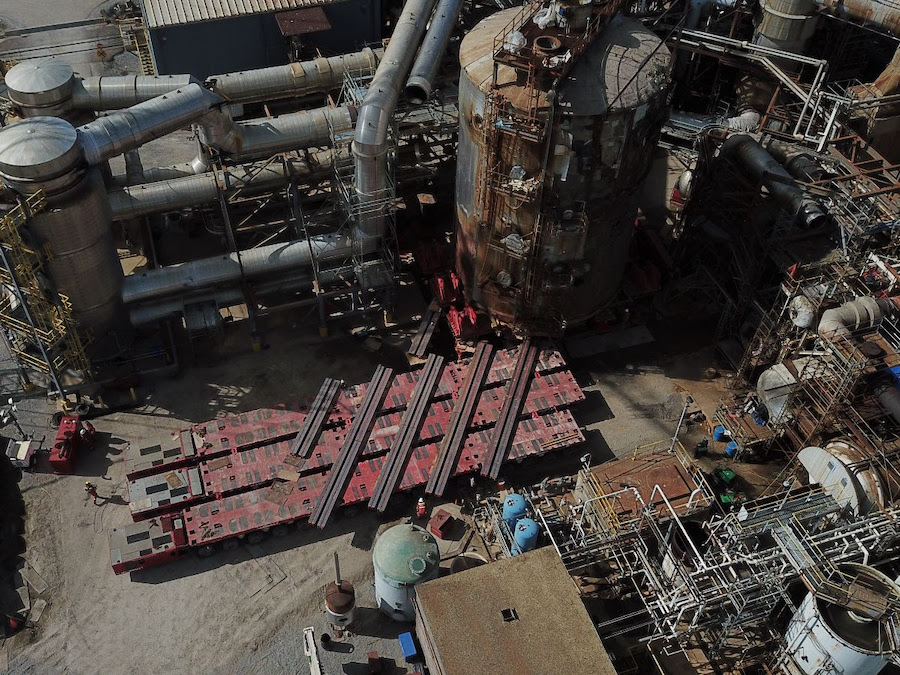
Mammoet was recently called on by a Gulf Coast spent acid regeneration facility to replace an aging acid converter vessel. Built several decades ago, the exchange of this 750-ton converter vessel was a critical part of an upgrade to the plant. The project needed to be executed within restricted available space and with as little disturbance as possible to nearby components and units that had been upgraded in a previous shutdown. The limited space, as well as strict ground bearing pressure requirements, made the use of heavy equipment challenging. So Mammoet devised a tailor-made cradling solution that could overcome these challenges and provide the precision and control to move the delicate vessel – a feat never attempted at this particular plant.
Historically, the exchange of converters is a time consuming and space intensive process, involving stick building and demolition that extends turnarounds and increases risks. In recent years, advances in technology have changed tank designs in such a way that new vessels can be moved in one piece. However, while the vessels now have this potential, they have very specific support conditions around their foundations that must be upheld to prevent damage to the sensitive internal linings of the converter.
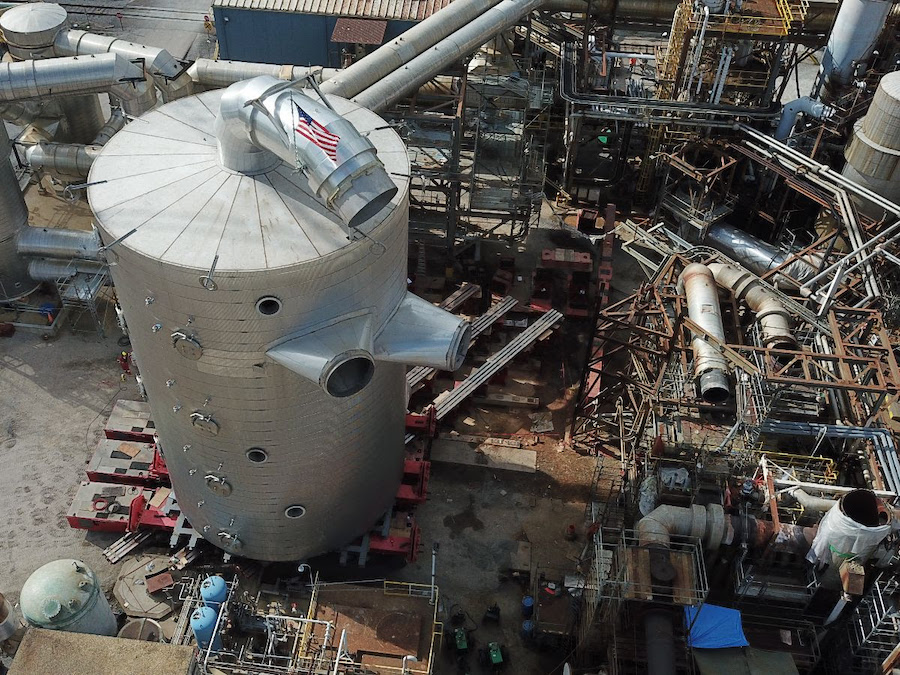
In response to these requirements, Mammoet designed a jack and slide system that could cradle both vessels by their foundations in order to elevate and slide them into place with the utmost control. In order to lift the vessels, Mammoet’s crew installed custom beams that were narrow enough to slide between the foundation and still have the capacity to cradle the entire 750-ton piece. These beams were then attached to jacking components set up on each side of the vessel and rested on a pair of 500 Te climbing jacks positioned at each end. First, to remove the old vessel, this complete arrangement was jacked up, lifting the converter in the process. It was then skidded out of the unit directly onto waiting SPMTs which had been placed under a total of 332 meters (1,090 feet) of skid track. The SPMTs then transported the vessel out of the facility.
Mammoet was then tasked with placing the new converter in the center of its foundation so the piping would align for proper installation. By reversing the operation method mentioned above, the team ensured that the new converter could be properly installed. This installation included aligning the skid track on SPMTs at precisely the right angle to ensure that the vessel would clear the steel of the existing unit by the allotted 2 ½ inches. Once cleared, the team positioned the trailers to ensure the skid tracks lined up with markers inside the unit and the converter’s rotation was correct before skidding the converter into its final position.