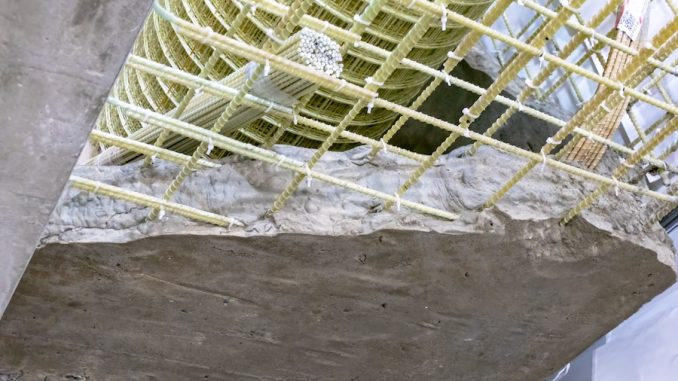
View the complete article here.
Concrete reinforcement is a cornerstone of durable construction—ensuring structures withstand tension, cracking, and environmental stresses. Traditionally dominated by steel rebar, the industry is now embracing innovative fiber reinforcement as a versatile alternative. This guide compares fibers and rebar—exploring their benefits, applications, and practical considerations to help contractors choose the best solution for their projects.
Understanding Concrete Reinforcement
Reinforcement enhances concrete’s tensile strength, which is naturally low despite its compressive strength. Rebar, or reinforcing bars, has long been the standard, providing robust support in beams, slabs, and foundations. Fibers, a newer innovation, are mixed into the concrete to distribute strength evenly, offering an alternative for specific applications. Both methods aim to prevent cracking and extend service life, but their approaches differ significantly.
Traditional Rebar: Strengths and Limitations
Rebar, typically made from carbon steel, is placed in a grid or cage within concrete forms before pouring. Its key strengths include:
- High tensile strength: Capable of handling heavy loads, making it ideal for large-scale structures like bridges or high-rise buildings.
- Customizable placement: Can be tailored to specific stress points, enhancing structural integrity in critical areas.
- Proven longevity: Decades of use demonstrate reliability when properly installed and maintained.
However, rebar has limitations:
- Corrosion risk: Exposure to moisture or salt can lead to rust, weakening the concrete over time.
- Labor-intensive: Cutting, bending, and tying rebar requires skilled labor and increases project time.
- Cost: Material and installation costs can escalate, especially for complex designs.
Fiber Reinforcement: A Modern Alternative
Fiber reinforcement involves adding synthetic, steel, or natural fibers (e.g., polypropylene, glass, or basalt) to the concrete mix. These fibers, ranging from 0.5 to 2 inches in length, enhance performance in unique ways:
- Crack control: Fibers bridge micro-cracks, reducing shrinkage and thermal cracking during curing.
- Ease of use: Mixed directly into the batch, they eliminate the need for manual placement, speeding up construction.
- Corrosion resistance: Synthetic fibers, unlike steel rebar, don’t rust, making them suitable for harsh environments.
Limitations include:
- Lower load capacity: Fibers are less effective for heavy structural loads compared to rebar.
- Uniform distribution: Effectiveness depends on even mixing, which can be challenging with inconsistent batching.
- Cost variability: While initial costs may be lower, high-performance fibers can be expensive.
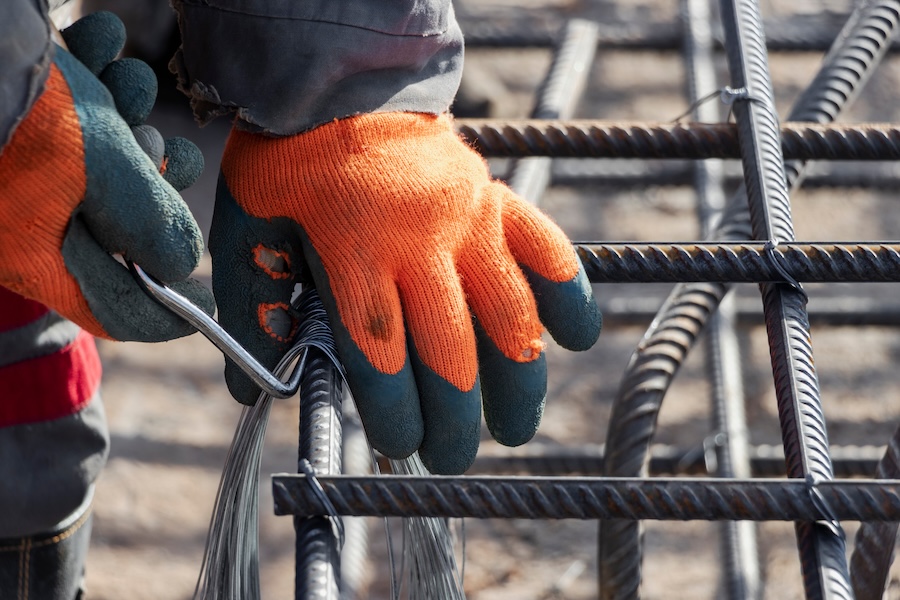
Types of Fibers
- Synthetic fibers: Polypropylene or polyethylene fibers are lightweight, corrosion-resistant, and ideal for slabs or overlays.
- Steel fibers: Offer higher strength, used in industrial floors or precast elements, but may corrode if not properly coated.
- Natural fibers: Emerging options like bamboo or jute provide eco-friendly reinforcement for non-structural uses.
Applications and Project Suitability
- Rebar: Best for structural elements like columns, beams, and foundations in commercial buildings or infrastructure. It’s the go-to for projects requiring high load-bearing capacity, such as highway overpasses.
- Fibers: Excel in non-structural applications like sidewalks, warehouse floors, or shotcrete for tunnels. They’re also popular in residential slabs where crack resistance is key.
Hybrid approaches, combining rebar with fibers, are gaining traction for projects needing both strength and crack control, such as parking garages.
Equipment and Installation Considerations
- For rebar: Requires cutters, benders, and tie wire, plus skilled labor to assemble cages. Concrete placement must avoid disturbing the rebar grid.
- For fibers: Needs precise dosing equipment (e.g., fiber dispensers) and mixers capable of uniform distribution. Portable batch plants can integrate fibers efficiently with proper calibration.
Contractors should ensure equipment compatibility and train crews on mixing techniques to avoid clumping or uneven fiber dispersion.
Cost and Efficiency Comparison
- Rebar: Initial costs range from $0.50 to $1.50 per linear foot, with labor adding $1-$3 per square foot. Installation delays can increase expenses.
- Fibers: Costs vary from $5 to $20 per cubic yard of concrete, depending on fiber type, but reduce labor and time, potentially lowering overall project costs by 10-15%.
For small projects, fibers may save money; for large structural work, rebar’s durability justifies the investment.
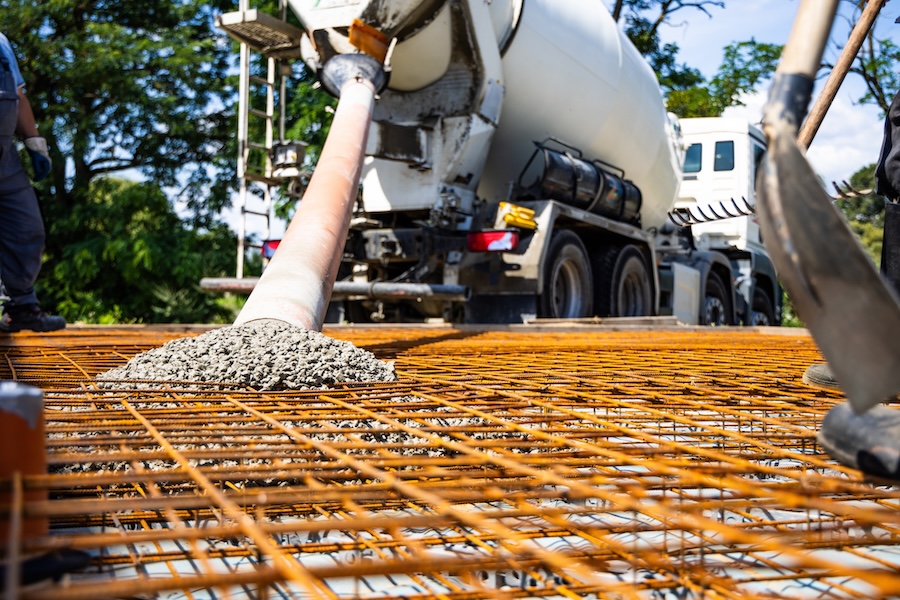
Environmental and Sustainability Impact
Fibers, especially synthetic ones, reduce the need for steel production, lowering the carbon footprint. Recycled fibers further enhance sustainability. Rebar, while recyclable, requires energy-intensive manufacturing, making fibers a greener choice for environmentally conscious projects.
Choosing the Right Option
- Project scale: Use rebar for heavy-duty, load-bearing structures; fibers for lighter, crack-sensitive applications.
- Budget: Evaluate labor savings with fibers against rebar’s long-term durability.
- Environment: Opt for corrosion-resistant fibers in coastal or humid regions; rebar with coatings in similar conditions.
Consult structural engineers to blend both methods where benefits overlap, ensuring compliance with local codes.
View the complete article here.
Is fiber reinforcement stronger than rebar?
No, fibers help control cracks but rebar is stronger for heavy load-bearing structures.
When should I use fibers instead of rebar?
Fibers are best for slabs, floors, sidewalks, and projects where crack resistance and speed are priorities.