
View the complete article here.
For prospective riggers and operators, an understanding of how to properly use slings and identify sling deficiencies during pre-use inspections is paramount.
Because slings typically handle loads under less than ideal circumstances, and in conjunction with equipment of varying ages, extreme caution should always be exercised during their use. Adherence to a host of general operating practices will ensure safe lifts and reduce the likelihood of sling damage.
Overall, the weight of a load should always be within the rated capacity of a sling, with sling angles of 45 degrees or less and shock loading to be avoided. Any sharp corners in contact with a sling should be padded, as failure to do so will permit edges of an item to cut into the sling.
Slings must not be shortened or lengthened via knotting, twisting, or with wire rope clips unless such a practice is approved by the manufacturer. When storing slings, you should always select an area that will not be subjected to mechanical damage, corrosive action, moisture, or extreme heat.
Three primary types of slings exist, with each boasting its own advantages.
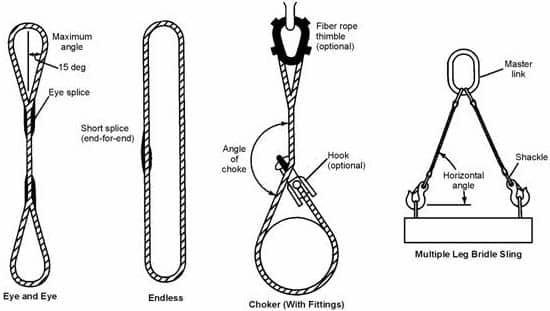
Wire Rope Slings
Known for their great strength and flexibility, wire rope slings don’t wear as rapidly as other types. The core, wire, and strand represent the three components that comprise a wire rope sling.
The core serves as the foundation that holds the rope together, and is either comprised of fiber, wire strand, or an independent wire rope, the latter being the strongest option. Wires are usually made of carbon steel and laid helically around the core in order to form a strand. Typically, 16 to 26 wires comprise a strand, with six strands rotated together in a clockwise direction to form a wire rope.
Every rope is subject to fatigue from bending stress during its use. To avoid fatigue, wires must bend repeatedly under stress, as when a rope passes over a sheave, without showing signs of wear or deformation.
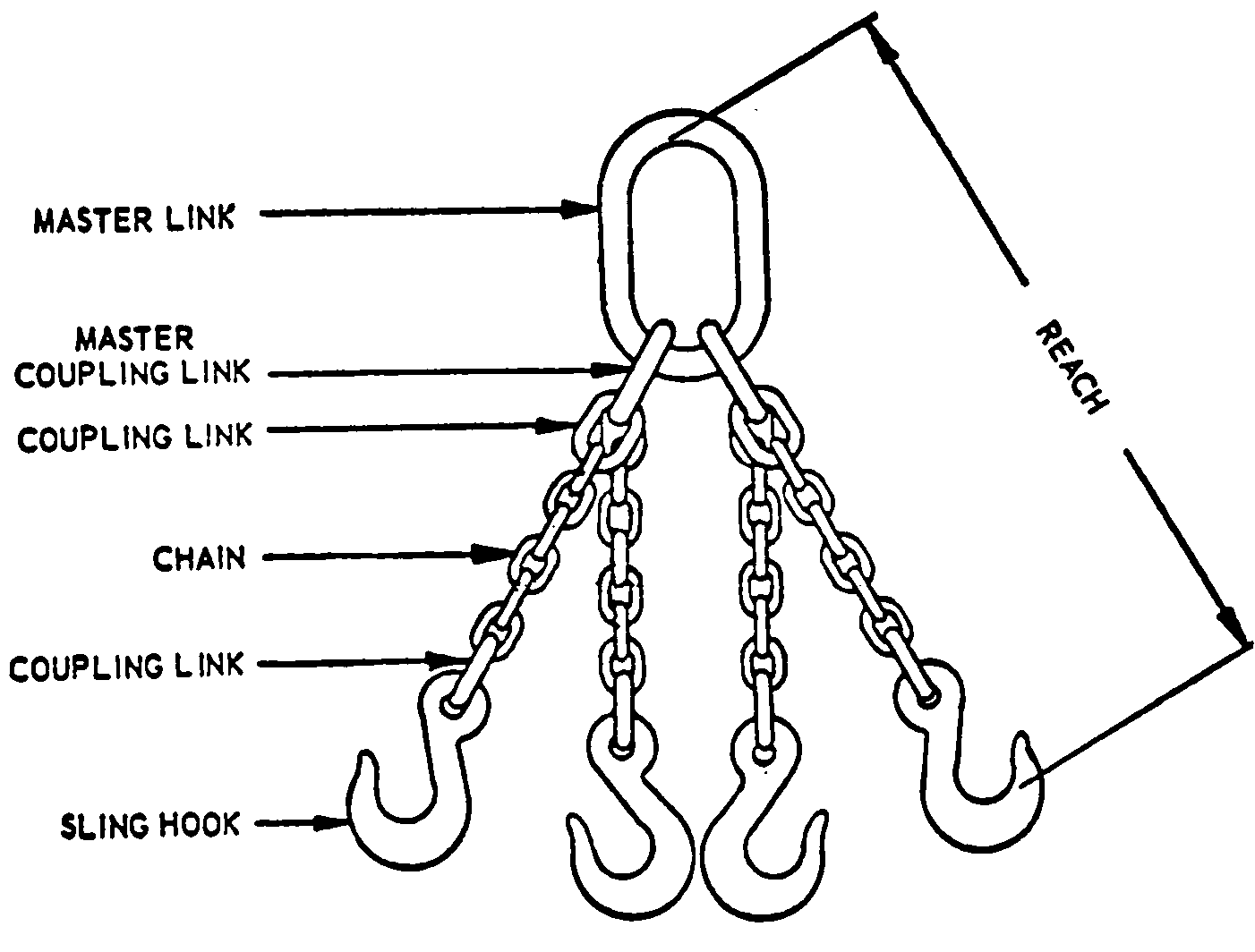
A rope made of many wires will feature greater fatigue resistance than a similarly sized rope made of fewer, larger wires, as smaller wires bend more easily when a rope passes over sheaves or around drums.
Because wire rope slings lose strength gradually due to natural causes, operators and riggers must determine a rope’s safe working load prior to use. This is achieved by dividing the rope’s breaking strength by five, which provides for a margin of safety as new rigging hardware is utilized.
The daily, pre-use inspection of ropes is of utmost importance, with the person utilizing the sling being responsible for performing a visual review. This person should initially look for broken wires, severe localized abrasions, scraping, and deformed end attachments. Kinking, corrosion, or other damage resulting in permanent rope distortion should also be noted, with the rope being removed from service as a result of such wear.
Synthetic Web Slings
Pliable and able to mold around shapes, synthetic web slings are comprised or either nylon or polyester. Nylon slings are most commonly used and feature an elastic stretch of 6 percent at their noted capacity. Polyester slings feature 3 percent stretch, which allows for a cushion against sudden shock. The size of either synthetic sling is determined by the width of the web.
While flexible, these slings are sensitive to heat and should never be exposed to temperatures exceeding 180 degrees Fahrenheit. They should also never be utilized in areas exposed to radiation. Instead, metal mesh slings capable of withstanding abrasive or hot loads should be utilized in such instances.
Operators inspecting web slings should first look for any signs of fabric discoloration resulting from melting, charring, or caustic attack. Any part of the sling showing such damage is enough of a reason to remove the sling from service.
When holes, tears, or cuts are identified on web slings, it’s a judgement call whether to take the sling out of service. An inspection of a sling’s inner threads will determine what action should be taken. If signs of wear or damage are identified, the sling must not be used, as the inner threads compose 80 percent of a sling’s strength. If red guard warning yarn is exposed, the sling must be removed.
The appearance of frayed fibers on the surface of the webbing should also be noted, as this is a sign of excessive abrasive wear commonly caused by load slippage in the sling.
Any sling featuring knots should not be used, as they reduce a sling’s capacity. Broken or worn stitching in load bearing splices can also cause significant reduction of sling capacity.
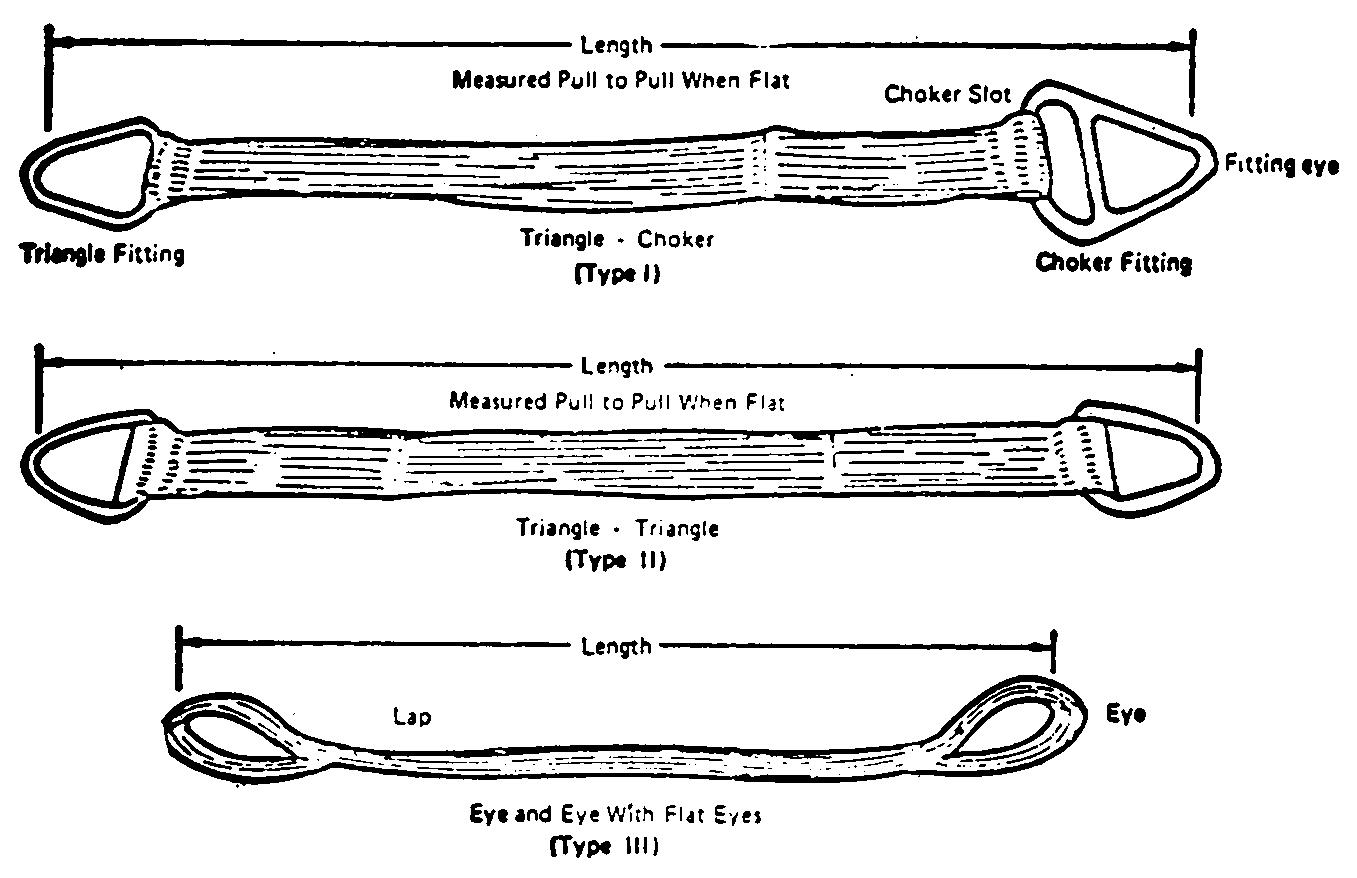
Chain Slings
Made of alloy steel, chain slings are best suited for lifting rough loads and withstanding high temperatures; however, they must be inspected and utilized carefully, as the failure of a single link of chain can cause an accident.
When looking for defects, eye a chain sling’s overall length and determine if it matches the length on the inspection tag. If the sling is shorter or longer, taking into account allowable tolerances, it must be taken out of service.
A check of the master link, connecting link, and the accompanying chain links for signs of elongation, wear, bends, or deformation is also mandatory prior to a chain sling’s use.
Hitches
Hitches are frequently used in hoisting operations to aid slings.
A straight hitch uses a single sling to connect a lifting hook to a load. When a hitch is in operation in this fashion, the full-rated lifting capacity of the attached sling may be utilized, but not exceeded. A tagline should also be used to prevent load rotation, which could damage the sling.
When two or more slings are attached to the same lifting hook, the total hitch becomes a bridle, with the load distributed among the individual slings. When creating bridle hitches, the sling angles must be carefully determined to ensure that the legs are not overloaded. To distribute the load equally, adjustment of the leg lengths with turnbuckles or chain lever hoists may be necessary.
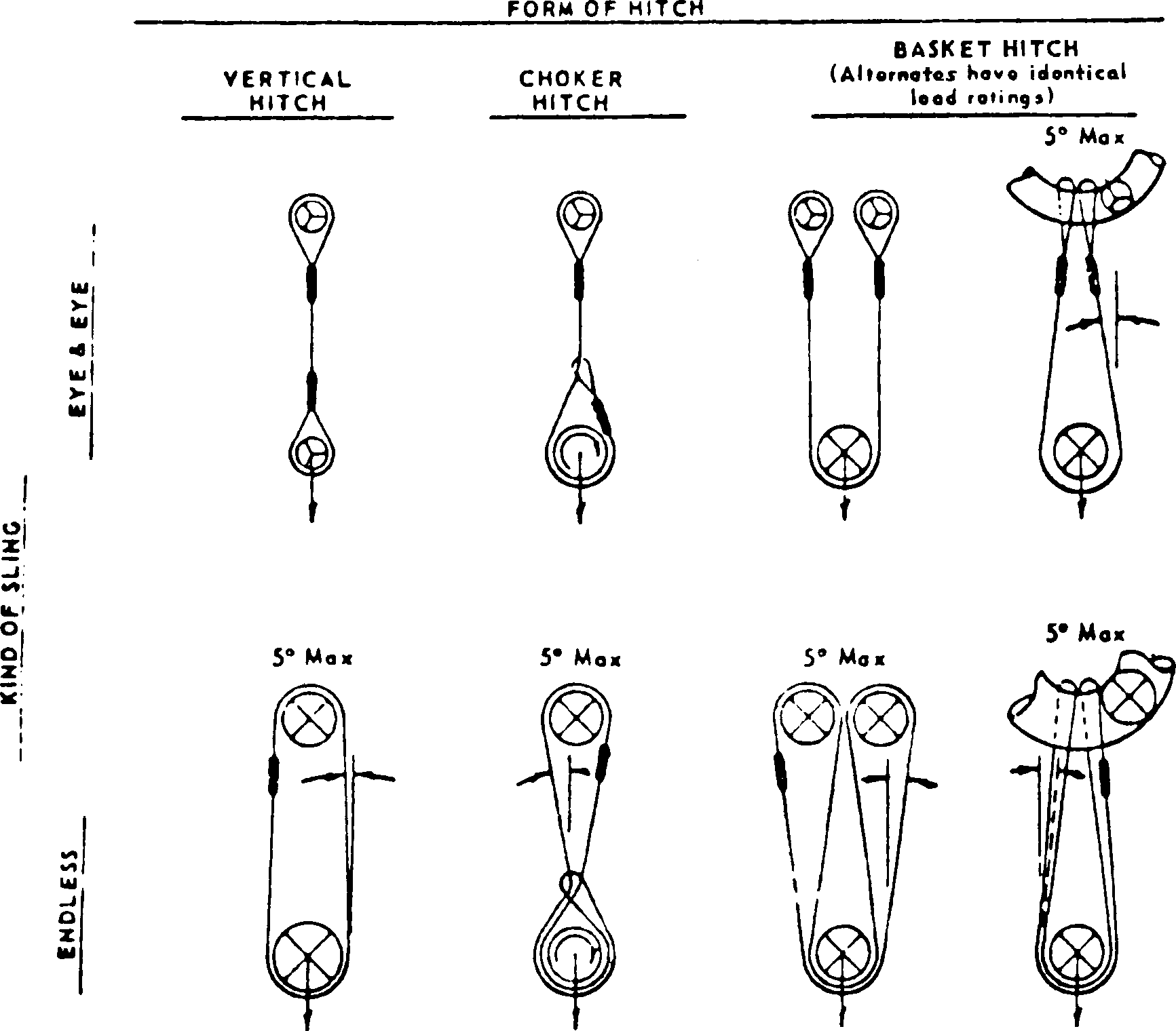
A basket hitch is used to distribute a load equally between two legs of a sling. The capacity of a sling used in a basket is affected by the bend or curvature where the sling body contacts the load.
When a lift requires the sling to be snug up against the load, a choker hitch is utilized. The choker must be pulled tight on the rope body, not the choker fitting, before a lift is made. It is recommended that operators use more than one choker hitch when lifting a load that might shift or slide during movement.
Because slings’ overall role in the lifting and movement of various loads is unlikely to change moving forward, an in-depth understanding of how to properly utilize and inspect slings remains a requirement for any operator wishing to conduct safe hoisting operations.
View the complete article here.
What are the key considerations for using wire rope slings in hoisting and rigging?
Considerations include checking for broken wires, abrasions, kinks, corrosion, or other damage during daily pre-use inspections, determining safe working load by dividing breaking strength by five, and addressing any visible wear or deformation promptly.
How should operators inspect synthetic web slings, and what signs indicate the need for sling removal?
Operators should inspect for fabric discoloration, holes, tears, cuts, frayed fibers, knots, and worn stitching. Any signs of damage or wear, including exposed red guard warning yarn or inner thread damage, warrant sling removal from service.