
Lubricants, oils, and greases are a crucial component in the operation of construction equipment. Despite their popularity, we find that they are often misunderstood—as well as used improperly. For that reason, we’ve composed this guide, which—we feel—is the most crucial, up-to-date information for lubricants, oils, and greases.
Lubricants
Lubricants are used to reduce friction and wear between moving parts in construction equipment and play a crucial role in maintaining the performance and efficiency of the equipment—as well as extending the lifespan of the equipment.
It’s important to note that construction equipment typically requires different types of lubricants—including hydraulic oil, engine oil, gear oil, and grease. The type of lubricant used depends on the specific requirements of the equipment and the operating conditions, such as load capacity and operating temperature—just to name a couple of examples.
Lubricants are typically applied to moving parts through various methods—particularly by manual application, spray application, or by using an automatic lubrication system. Whatever method you use, it is essential that you follow the manufacturer’s recommended lubrication schedule to ensure that the equipment receives the proper amount of lubricant at the correct intervals.
Are lubricants ever used incorrectly? Yes, on a frequent basis, actually. The wrong type of lubricant is used for the equipment. Equipment is over-lubricated—or under-lubricated. Sometimes the lubricant is not replaced at the recommended intervals. Whatever the scenario may be, the incorrect usage of lubricants can result in reduce performance, increased wear-and-tear, and reduced service life of the equipment.
In recent years, more-and-more equipment owners are starting to use lubricants that are considered to be better for the environment—such as biodegradable oils and Environmentally acceptable Lubricants (EALs). These products are made from natural, renewable resources and are designed to biodegrade into harmless substances when exposed to the environment.
Are EALs as effective as traditional lubricants? Yes. Despite the fact there was some initial resistance from “old school” equipment owners, EALs are now considered to offer high performance and stability compared to traditional lubricants and are a go-to option for use in construction equipment that is used in environmentally sensitive areas.
EALs are becoming essential to the construction industry—improving the environmental impact of equipment, ensuring that contractors are complying with regulations, and—at times—even offering lower costs for equipment owners to keep their equipment on a solid lubrication schedule.
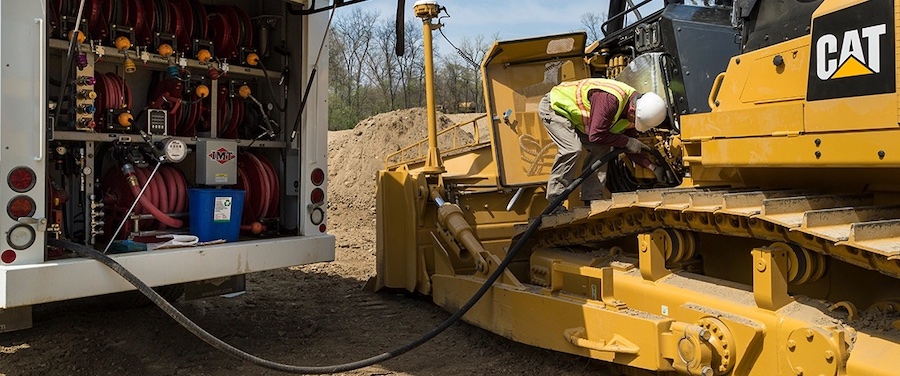
Oils
Although the terms are often used interchangeably, oils and lubricants have different meanings.
Oil is a broader term that refers to any fluid that is used to lubricate and protect mechanical components—including engines, transmissions, hydraulic systems, and gearboxes.
Lubricants, on the other hand, are a specific type of oil that is created with specific additives and properties to enhance their performance and provide additional benefits—such as improved wear protection, better heat dissipation, and resistance to contamination. Consider how biodegradable hydraulic fluids are specifically designed to lubricate and protect the hydraulic systems of excavators—providing reliable performance while reducing the impact on the environment.
So—you could say that all lubricants are oils, but not all oils are lubricants.
Some of the most common applications for construction oils include:
- Engine oils: Engine oils are used to lubricate and protect the internal components of engines—such as pistons, bearings, and valve trains.
- Transmission oils: Transmission oils are used in the transmissions of construction equipment to provide lubrication and protection to gears, shafts, and other moving parts.
- Gear oils: Gear oils are used in gearboxes and differentials to provide lubrication and protection to gears and bearings.
- Hydraulic oils: Hydraulic oils are used in hydraulic systems to transfer power and provide lubrication to moving parts.
- Drivetrain oils: Drivetrain oils are used in the drivetrains of construction equipment—such as bulldozers and excavators—to provide lubrication and protection to gears, shafts, and other components.
- Circulating oils: Circulating oils are used to lubricate and cool large equipment—such as cranes and drilling rigs—by circulating through hydraulic systems and heat exchangers.
Instances were oils are typically used improperly with construction equipment include using the wrong oil for a specific application, not maintaining proper oil levels, and failing to replace oil and oil filters at the recommended intervals.
What happens when oils aren’t used properly? Improper oil usage can result in increased wear and damage to various components, decreased performance and efficiency, as well as increased downtime and maintenance costs.
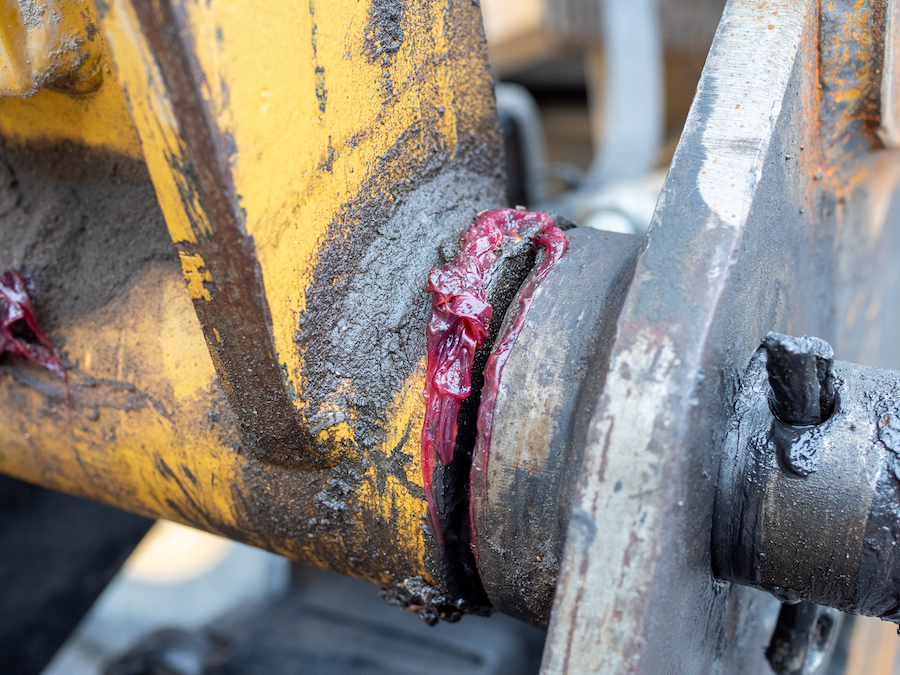
Greases
Like lubricants and oils, greases are also a term that is often used interchangeably but—in fact—has a different meaning. Although each is used to reduce friction and wear in construction machinery, they each differ in their composition and application.
Greases are semi-solid lubricants that are composed of a base oil and a thickener. Greases are used in applications where a continuous supply of lubricant is required—such as hinges, chains, and gears. Greases are typically applied using a grease gun and are designed to stay in place for an extended period of time—providing a consistent and continuous supply of lubrication.
Like lubricant and oils, greases are also used improperly on a regular basis. Some of the most common mistakes include:
- Incorrect grease selection: Using the wrong type of grease for a particular application can result in poor performance or can even cause damage to the equipment.
- Over-application: Applying too much grease can cause excessive pressure buildup and can eventually cause component failure or bearing damage.
- Mixing different types of greases: Mixing different types of greases can result in a reduction in the performance and stability of the grease—leading to increased wear and reduced protection.
- Improper storage: Greases that are stored in an environment that is too hot or too cold can cause the grease to degrade—reducing its performance and stability.
- Infrequent re-lubrication: Neglecting to re-lubricate components in a timely manner can result in increased wear and reduced performance of the equipment.
FAQs
What is the shelf life of construction equipment lubricants and oils? Is it different for biodegradable lubricants?
The shelf life of construction equipment lubricants and oils varies—ranging from 2 to 5 years for traditional oils and potentially shorter for biodegradable options. Factors such as storage conditions and exposure to air, light and temperature affect shelf life. Biodegradable lubricants may have shorter shelf life due to their complex formulation. Of course, you should always check the manufacturer’s specifications for specific information.
How often should construction equipment be lubricated? Do biodegradable hydraulic oils have to be changed more often than traditional lubricants?
How often construction equipment should be lubricated depends on factors like the type of equipment, operating conditions, and manufacturer’s recommendations. That being said, it is typically recommended to lubricate daily or every 50 hours of operation. Biodegradable hydraulic oils may not necessarily need to be changed more often than traditional lubricants, but the frequency of changes may depend on the specific oil and operating conditions. As previously mentioned, it’s always ideal to consult the manufacturer’s recommendations for accurate information on lubrication frequency.
Will biodegradable lubricants biodegrade my construction equipment?
No, biodegradable lubricants are designed to biodegrade after they are disposed of or spilled—not while they are being used to lubricate construction equipment. They are formulated to perform similarly to traditional lubricants while in use, but are intended to have a lower environmental impact once they are no longer needed.
What are some common misconceptions about lubricants, oils, and greases used for construction equipment?
Some common misconceptions about lubricants, oils, and greases for construction equipment include the idea that all lubricants are the same, that they can be mixed without consequence, and that using more grease is always better. These misconceptions can lead to improper maintenance and potential damage to equipment.
How can one properly use lubricants, oils, and greases for construction equipment?
Proper use of lubricants, oils, and greases for construction equipment involves understanding the specific requirements of each piece of machinery and using products designed to meet those needs. It's important to follow manufacturer guidelines on types of lubricants and frequency of application. Regular maintenance checks are also essential to ensure the lubricants are performing their function of reducing friction and wear, and to prevent issues like contamination.