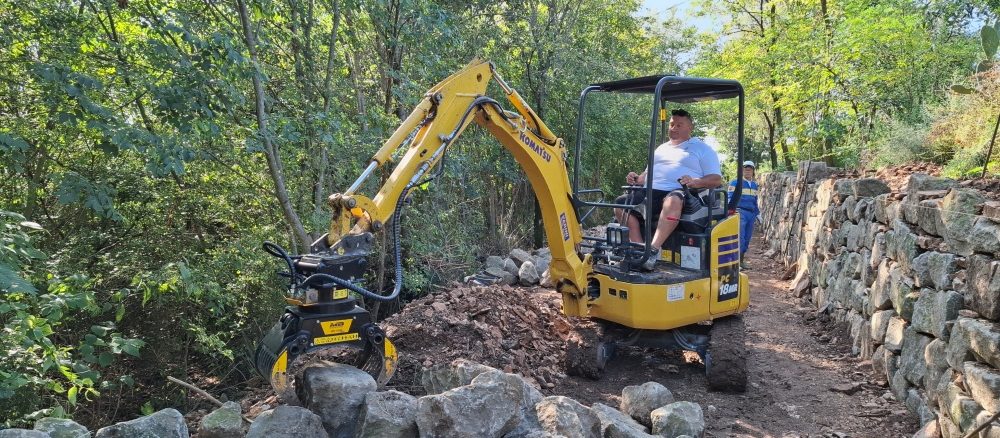
Dry stone walling is a traditional construction technique rooted in many cultures around the world, especially common in Europe. These structures are crafted without any binding agents, relying on the precise interlocking of stones, where the weight and precise placement of each stone are used to create durable and resilient barriers. In addition to defining boundaries and shaping landscapes, they serve important ecological roles: they protect against desertification and soil erosion, help prevent landslides, and provide shelter for a range of animal and plant species.
Despite the benefits of these structures, building and maintaining dry stone walls requires significant skill and meticulous attention to detail, making skilled labourers increasingly rare and valuable. The guardians of this tradition must carefully select and place each stone to ensure stability and longevity. However, thanks to technological advancements, even these traditional techniques can now be enhanced by equipment that simplifies construction, speeds up the process, and delivers maximum precision with minimal effort—handled by a single operator seated in a machine.
MB Crusher’s MB-G selection grabs step in to lend a hand, enabling operators to grip, move, and position stones of all shapes and sizes with exceptional accuracy, precision, and safety.
As Mr. Ivanovich, owner of Battaglia Costruzioni in Italy, shared, “Purchasing the MB-G350 selection grab was a game-changer for us—we can do whatever we want.” Currently working in a hilly park, he is building a dry stone wall with the local stone -Euganean trachyte- a highly durable stone also used to pave much of Venice’s walkways.
In just four days, with the MB-G350 selection grab, Mr. Ivanovich managed to process 42 cubic metres of trachyte, creating a 52-metre-long dry stone wall averaging 160 cm in height. Manually, this would have required at least five workers and 35–40 days of labour.
Excitedly, he adds: “Opening and closing the grab is incredibly simple. After only ten minutes, the machine works as if it’s been in operation for months. You can even work with fine precision, slotting the stone exactly where you want it, turning it… you can do whatever you need to. It’s uniquely simple.”
The MB Crusher grab is also ideal for constructing riprap embankments, commonly used along rivers in both mountainous and flat areas. These embankments vary by function but generally aim to protect banks from erosion and to control water levels. Here too, this isn’t a matter of merely piling stones but rather a painstaking process made easier, more precise, and safer with the MB Crusher selection grab.
Dry stone walls have been recognised as a UNESCO World Heritage asset, but they need to be “kept in practice”—enabled, passable, feasible, and sustainable, not just preserved as museum pieces.
The combination of ancient techniques and modern equipment like MB Crusher’s MB-G grabs represents the future of dry stone walling and riprap embankments. With the support of MB Crusher’s equipment, we can sustain a centuries-old tradition while achieving high performance, safety, and respect for the environment.