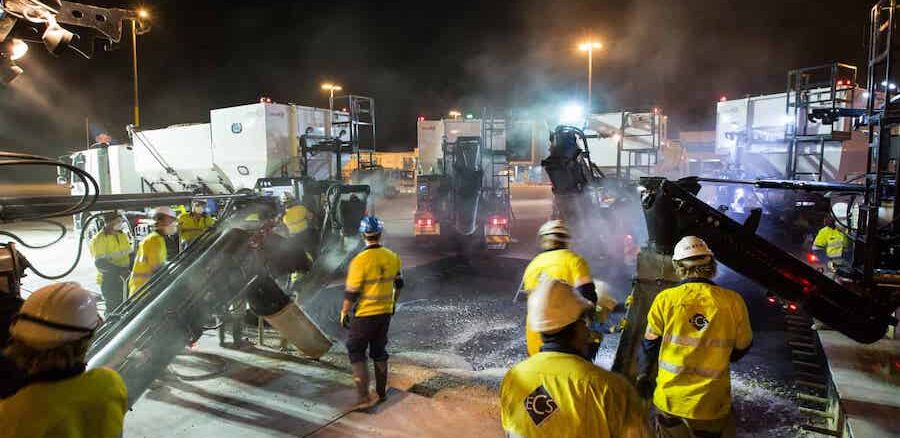
View the complete article here.
The traditional drum was invented in the early 20th century to meet the construction industry’s need for consistent, large-scale concrete production. Typically used in large construction sites and infrastructure projects, these mixers ensure a uniform mix of concrete in considerable volumes.
However, sometime in the mid 1960s, the volumetric mixer was introduced. This mixer was designed to address the drum mixer’s limitations, such as potential wastage and lack of on-site adjustability—it stores raw materials separately and mixes them on-site in precise quantities, offering flexibility in adjusting the mix as required.
So, which is the better option?
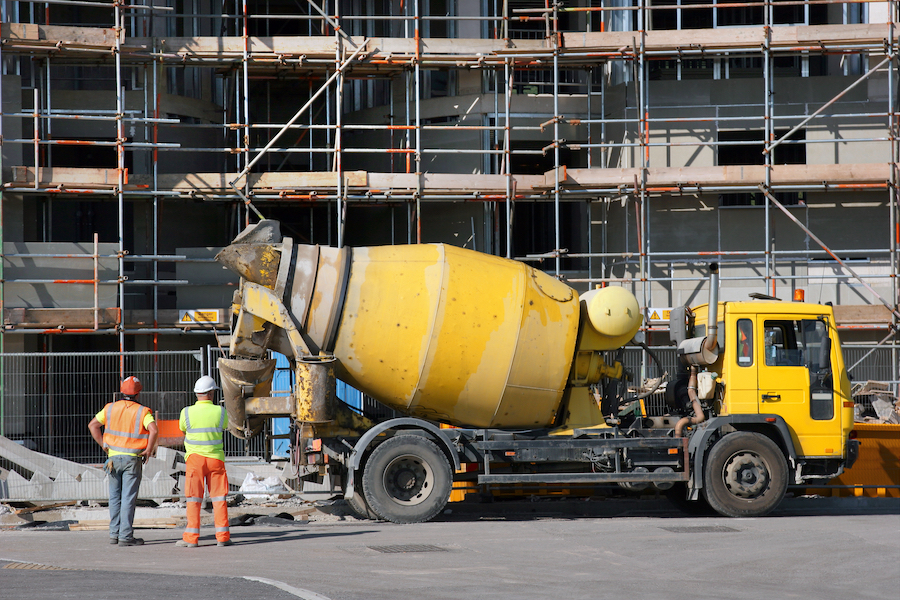
Traditional Drum Mixer Pros and Cons
The traditional drum mixer is essentially a revolving drum into which concrete components—cement, aggregates, and water—are loaded in a pre-defined sequence. As the drum rotates, these components are mixed together to produce concrete.
As a crucial piece of equipment in the construction industry for almost a century, traditional drum mixers offer several advantages. Its primary strength lies in its ability to produce large, consistent batches of concrete—making it ideal for sizeable construction projects. The pre-mixed nature of the concrete ensures uniformity, which is essential for structural integrity in many applications. In addition, these mixers are often more straightforward in design—which can make them more durable and easier to maintain over extended periods.
However, there are also some drawbacks associated with traditional drum mixers. One significant limitation is the potential for the concrete to start setting if not used promptly, especially if there are unforeseen delays on the construction site. This can lead to wastage, as once the concrete begins to set, it can’t be reused. The fixed batch size also means there’s a potential for overproduction, which not only wastes materials but can also be costly. In addition, any adjustments to the mix—such as changes in water content or additives—must be decided upon in advance and can’t be altered on the spot, limiting the mixer’s flexibility in variable conditions.
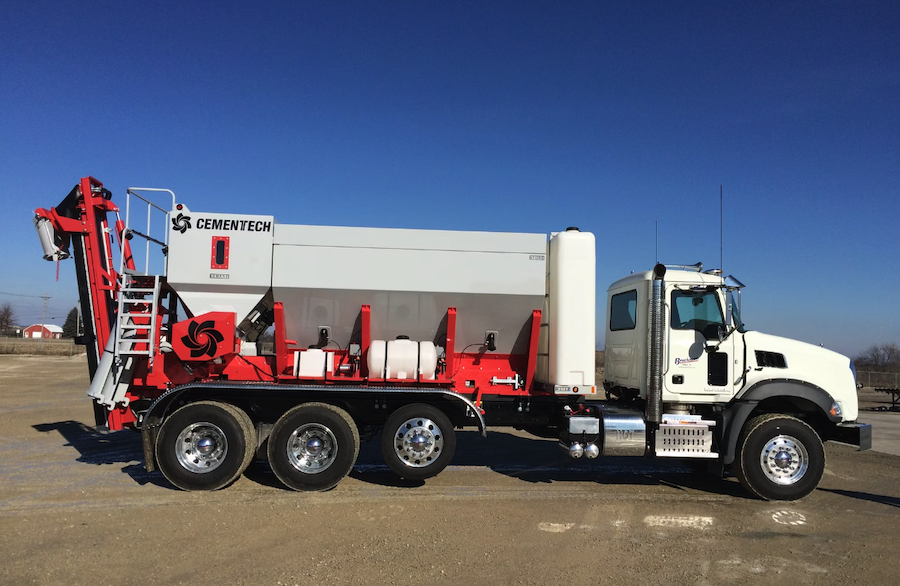
Volumetric Mixer Pros and Cons
The volumetric mixer contains separate compartments for different components. The mixing occurs on-site, with materials combined in the exact quantities required—allowing for a fresh mix on demand.
As a relatively newer innovation in the construction industry, the volumetric mixer offers a unique set of advantages tailored to modern construction needs. These mixers have the ability to produce precise volumes of concrete on-site, effectively reducing wastage. Because materials are stored separately and mixed only when needed, there’s a flexibility to adjust the mix based on immediate requirements—a significant advantage for projects with changing specifications. In addition, the just-in-time mixing approach ensures that the concrete is always fresh—potentially leading to better overall quality.
However, volumetric mixers—while versatile—can pose challenges in maintaining a consistent mixture. The quality of the mix often hinges on the expertise of the operator and the maintenance condition of the machine. Compared to the more straightforward operation of traditional drum mixers, volumetric mixers might produce varying results—especially when large quantities are involved.
Comparing Operation and Efficiency
Traditional drum mixers and volumetric concrete mixers differ significantly in their operation, each with its own set of advantages and challenges. In terms of ease of operation, traditional drum mixers might be seen as more straightforward—especially for those who have worked construction for a long period of time. The process involves loading the concrete components in a predefined sequence and allowing the drum to mix them. Volumetric mixers, on the other hand, require a more nuanced approach. Operators must understand how to mix components in real-time—tailoring to the specific needs of the moment, which can pose a steeper learning curve for some.
In terms of efficiency, volumetric mixers can offer an edge—especially for projects where the required concrete volume or mix might change frequently. Since they mix on-site and on-demand, there’s a reduction in wastage and always a fresh batch of concrete available.
Operation costs can vary. Volumetric mixers might have higher initial costs, but they can lead to savings in the long run by reducing material wastage and offering precise mixes. Maintenance-wise, while both machines require regular upkeep, the more complex design of the volumetric mixer might entail more frequent or specialized maintenance checks.
As for return on investment, it depends on the circumstances. For larger projects requiring consistent, high-volume concrete batches—a drum mixer might offer a better ROI. However, for diverse projects where flexibility and adaptability are paramount, a volumetric mixer—despite its higher initial cost—is likely to prove more economical in the long run.
Comparing Applications and Suitability
Traditional drum mixers excel in environments that demand consistent, high-volume concrete batches. Large-scale construction projects—such as skyscrapers, bridges, or highways—benefit from the drum mixer’s ability to produce large, uniform batches of concrete in a single mix. This ensures consistent quality and pace, crucial for projects where timeframes are tight and margins for error are small.
Volumetric concrete mixers prove to be most beneficial in more dynamic environments that require adaptability. They’re especially suited for projects where the volume or mix specification may change frequently or on short notice. This could range from smaller construction tasks, repairs, and renovations to larger projects in remote locations where logistical challenges make it hard to estimate exact concrete requirements. The on-site, on-demand mixing capability of volumetric mixers means less waste, the ability to adjust the mix in real-time, and the production of fresh concrete as and when needed. This makes them particularly valuable for projects that don’t have the luxury of exact upfront specifications or where changes are part and parcel of the task.
In essence, while both mixers can be used across a variety of applications, traditional drum mixers are the go-to for large-scale, consistent production—whereas volumetric mixers are the choice for flexible, adaptive, and varied projects.
Comparing Costs
When evaluating the costs associated with traditional drum mixers and volumetric concrete mixers, several factors come into play—including the initial investment, operational expenses, and potential long-term savings.
Traditional drum mixers, being a staple in the construction industry for such a long period of time, typically have a more predictable cost structure. The initial investment for a drum mixer might be lower than that of a volumetric mixer. Operational costs, including maintenance, tend to be straightforward given the machine’s simpler design—although there can be costs associated with waste if the mixed concrete isn’t used promptly or if there’s overproduction.
Volumetric concrete mixers, on the other hand, often come with a higher initial price tag due to their more complex design and advanced features. However, the potential for long-term savings can offset this initial cost. Their on-site, on-demand mixing capability can drastically reduce material wastage. This can lead to significant savings, especially on larger projects or over an extended period. Furthermore, the ability to adjust mixes in real-time can prevent the costs associated with redoing parts of a project due to incorrect concrete specifications.
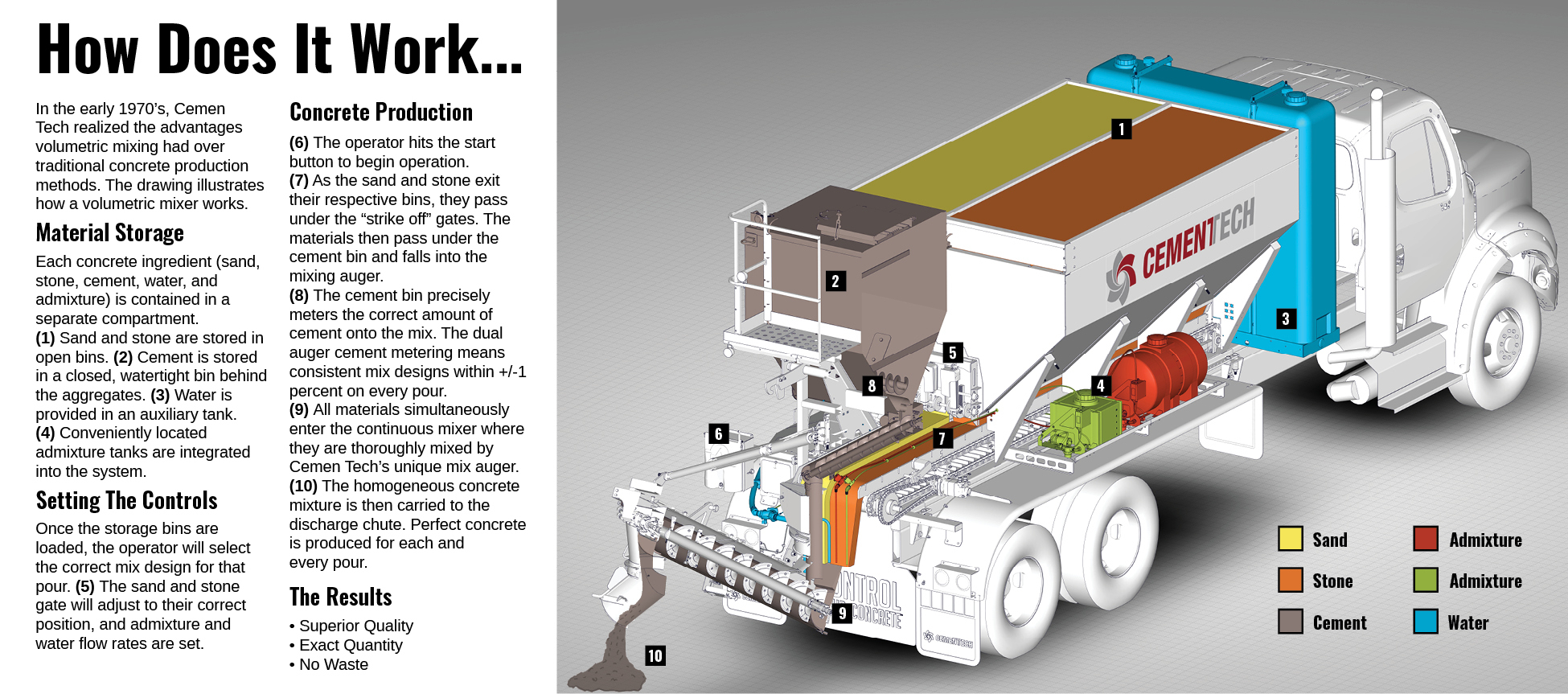
The Final Verdict
Of course, the final choice between traditional drum mixers and volumetric concrete mixers hinges on specific project needs and objectives. Drum mixers—time-tested and efficient for bulk, consistent production—continue to play an essential role in large-scale construction projects. However, as projects become more diverse and demand greater flexibility, the adaptability and precision of volumetric mixers offer undeniable advantages. While both mixers have their unique strengths and challenges, for a modern construction scenario with changing specifications and the need to minimize wastage, the volumetric mixer emerges as the more versatile and cost-effective option.
View the complete article here.
What are the advantages of traditional drum mixers?
Traditional drum mixers offer advantages such as producing large, consistent batches of concrete, simplicity in design, and suitability for high-volume construction projects.
In what scenarios are volumetric concrete mixers more beneficial?
Volumetric concrete mixers excel in dynamic environments where adaptability is crucial, making them suitable for projects with frequently changing concrete volume or mix specifications and providing on-site, on-demand mixing capabilities.