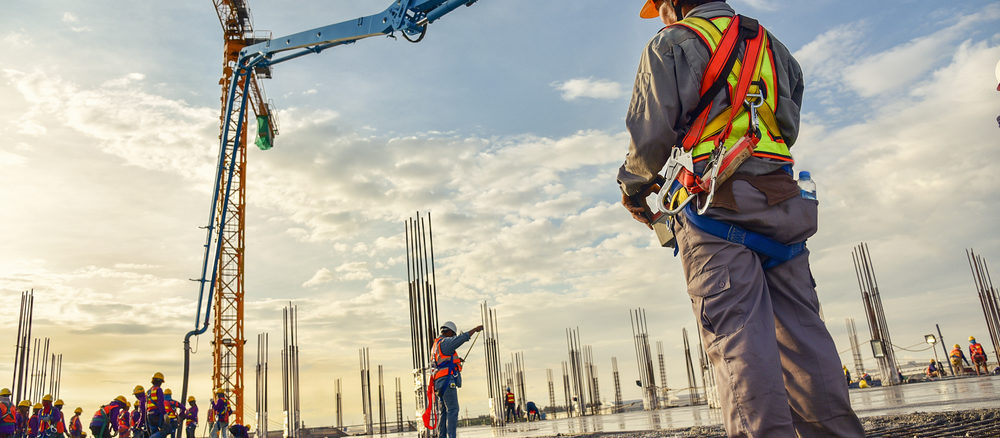
View the complete article here.
Understanding the critical properties of concrete ensures success in the mixing, transportation, placement, finishing, and maintenance of high-quality pavement. Requirements can change depending on the anticipated use of the pavement and the necessary functions of the area. So, it is important that the contractor, concrete provider, and property owner maintain open communication about the decisions and how these details will impact the outcome of the concrete.
Mixture Uniformity: What You Need to Know
When it comes to uniformity, the overall goal is to maintain a uniform surface even though you will be using variable materials. Environmental and material factors are always changing depending on the project. Even though these changes are expected, certain properties can be maintained for each batch. These efforts help to avoid preventable issues in the final product.
The properties of the materials need to be monitored during every step, with adjustments made to the proportions as needed. Instead of batching by volume, it is always best to batch by mass.
These are some of the factors that can affect uniformity:
- Raw Materials: The best results are available when all of the cement is sourced from a single lot.
- Batching Operations: Measuring the ingredients and adding them to the mixer should be completed by mass whenever possible.
- Mixing Operations: This step is necessary to ensure even distribution of the mixture ingredients.
A variety of tests can be used to measure the uniformity of the concrete. These tests might include unit weight, slump, coarse aggregate content, air content, compressive strength, and more. It is important to evaluate representative samples to assess the uniformity.
Concrete Workability
The term “workability” refers to the ease at which the concrete can be laid and compacted. Not only does good workability improve a contractor’s ability to place the fresh concrete. But, the workability also impacts the density after the concrete is hardened. Many industry experts agree that workability is an important measure of uniformity.
Several characteristics impact the workability of fresh concrete:
- Water Content
- Aggregates
- Cement
- Supplementary Cementitious Materials
- Entrained Air
- Admixtures
- Temperature
- Time
Not only is the right workability need for the environmental factors and end goals, but it is also important to evaluate how the workability will be affected by the tools that are used. If you experience changes in the workability of the concrete, then it is an indication that other factors are changing, such as the environment, proportions, or raw materials.
Common tests to measure the workability of the concrete include the slump test, compacting factor test, penetration tests, and the Vebe test.
Problems Due to Segregation of Concrete Materials
If the coarse aggregates in the concrete segregate from the mortar, then common problems can occur. Usually, this segregation causes the concrete to have poor durability and lower strength. It is likely that the concrete will crack and shrink, or the texture could be too harsh when the concrete is placed.
Luckily, it is easy to prevent segregation with the right preventive steps. The most important fact is to use well-graded aggregate. Also, watch the texture of the concrete when it is being placed. Can you see that the coarse aggregates move at a different pace than the finer particles and the mortar? This visible cue is easy to identify. If this problem is noticed, then it is essential to contact the batch plant as soon as possible so that the mix proportions can be adjusted.
Bleeding on Newly Placed Concrete
When concrete is newly placed, you might see the appearance of water on the surface of the concrete. The heavier particles settle, bringing water to the surface. A little bit of bleeding is helpful so that you can avoid cracking on the surface due to rapid evaporation of the water that causes the concrete to dry quickly.
When excessive bleeding occurs, there are often voids beneath the large aggregate particles. Additionally, the surface can soften due to the change in the ratio for the water-cementitious materials.
In ideal circumstances, the curing and finishing will occur after the bleeding is finished. This bleeding reaction can be reduced by increasing the amount of fine content and also using water-reducing admixtures and air-entraining particles.
Setting the Concrete
Eventually, the concrete will set, which means that the workability is lost because the concrete becomes hardened. The chemistry in the mixture will impact the speed of the setting. For example, if you need to slow the setting, then you might choose granulated blast-furnace slag or Class F fly ash. On the other hand, it is also possible for the setting to be accelerated based on the increase in temperature.
These factors are critical to the successful placement of the materials. The setting timeline affects the timetable for when the materials can be placed and finished. The joint sawing schedule also needs to be adjusted based on the setting time of the concrete.
Concrete Strength to Carry the Anticipated Loads
One false assumption in the industry is that the concrete strength is a good measure of the quality of the concrete. But, the strength isn’t the only factor that affects the durability and performance of the pavement.
Strength is the measurement that determines the ability of the concrete to resist forces or stresses and carry the anticipated loads. If increased strength is needed, then the ratio of water and cement needs to be adjusted. Additionally, higher temperatures accelerate the strength gain. An increase in air content can also play a part because higher air content results in decreased strength.
When testing for strength, it is important that look at the flexure (bending) and compression of the concrete. In most situations, the compressive strength is much stronger for concrete compared to the flexural strength.
It is possible to determine early strength on the job site by evaluating both temperature and time measurements. Testing needs to be done during the mix design stage as well as on-site with field tests. Depending on the mixture that is used, the strength of the concrete can be achieved anywhere from a few hours to a few days.
Poisson’s Ratio and the Modulus of Elasticity
As a general rule, the modulus of elasticity often correlates with the amount and type of aggregate, as well as the strength of the concrete. The measurement of the modulus of elasticity (also known as stiffness) of the concrete will determine how the materials will handle under load. These tests help to determine the risk of cracking.
Poisson’s ratio is a tool that is often used for the deflection measurements. Various factors can affect the elasticity, which are all the same factors listed above that affect concrete strength.
Important Factors to Consider for Concrete Durability and Performance
Here are important details that need to be assessed for concrete placement:
- Shrinkage: When the volume or length of the concrete decreases, then it is known as shrinkage. This problem usually occurs due to mechanisms during mixing and placement that affect moisture loss of the concrete. Often, shrinkage increases when there is higher water content in the concrete.
- Temperature Effects: The hydration of the concrete generates heat, which increases the risk of cracking. When the temperature increases, then the concrete expands. Then, the concrete shrinks again after the temperatures cool. The expansion and contraction vary depending on the type of aggregates that are used. If the temperature increases, then it will speed up the hydration rate and setting time. The challenge of placing concrete in the cold-water climates is preventing freezing so that strength can be gained.
- Permeability: If you want to improve the durability, then it is important to manage the penetration of fluids. Concrete permeability needs to be reduced, helping to decrease the risk of cracking and other common problems. The best strategies to reduce permeability is by adjusting the ratio of water-cementitious materials, increasing the hydration, implementing good curing practices, and using supplementary cementitious materials.
- Frost Resistance: In a cold weather climate, frost resistance is an essential factor to consider. If the pavement has problems with frost resistance, then there are risks due to freeze-thaw damage, D-cracking, salt scaling, and popouts. Several steps can help to improve the frost resistance, such as maintaining an air-void system to accommodate space for expanding water to move, achieving adequate strength, using quality materials, using good practices during every stage of mixing and placement, as well as protecting the concrete to ensure sufficient strength gain before exposure to freezing temperatures and salts.
- Sulfate Resistance: When sulfates come in contact with the concrete, a reaction can occur with the hydrated tricalcium aluminate. As a result, the expansive crystals of the infiltrating salts can damage the cement paste and cause cracking. These problems are more severe when the pavement is exposed to wet and dry cycles. To reduce the risk of sulfate attack, aim for low permeability and use a mixture that includes a low ratio of water-cementitious materials.
- Alkali-Silica Reaction (ASR): Concrete distress doesn’t always coincide with the presence of ASR gel. Several things can be done to control cracking and expansion due to ASR, such as using nonreactive aggregates, achieving the right blend, using the proper proportions of supplementary cementitious materials, and using blended cements or lithium compounds.
- Abrasion Resistance: The concrete needs to resist surface wear, which is known as abrasion resistance. This factor is important to ensure the right skid resistance and texture on the surface of the concrete. To improve the abrasion resistance, choose hard and strong aggregates, use concrete rated with a high compressive strength, and ensure the proper techniques for finishing and curing.
An Overview of Early Age Cracking
The moisture and temperature changes impact the expansion and shrinking of the concrete, which can lead to cracking when the shrinkage exceeds the strength of the concrete. One strategy to manage the location and number of shrinkage cracks is the timely placement of the joints, using the optimal depth and spacing.
With the right practices, it is possible to reduce the risk of cracking, including all common types of cracks: longitudinal cracks, random transverse cracks, plastic shrinkage cracks, map cracks, edge and corner cracks, and more.
These are some of the strategies used in the planning and placement stages to reduce early age cracking:
- Joint Placement: Most concrete pavements are jointed, helping to control the cracking. Strategic steps need to be taken to plan the location, number, and size of the contraction joints. Placing the joints creates a natural plane of weakness if the joints are sawed with the right depth, spacing, and timing.
- Curing Techniques: Specific steps need to be followed based on temperature control and moisture control that can impact the location and severity of cracking. These factors vary depending on the materials and environmental factors. Curing helps the concrete to develop strength before the onset of stresses due to shrinkage.
- Materials Selection: Shrinkage can be controlled with careful management of the mix design and the materials that are used. Optimize the amount and size of the coarse aggregate and avoid the excessive use of cementitious materials. Additionally, consider the use of water-reducing admixtures to prevent drying shrinkage.
- Moisture Control: Plastic shrinkage cracking can be prevented with moisture control. Early drying increases the risk of warping, which can lead to fatigue cracking. Moisture control is always an essential step to prevent cracking, and the best strategy is to use the right techniques for curing. After the concrete is finished, apply the curing compound as soon as possible. Also, an evaporation retarder can be applied to the surface of the concrete before the finishing is complete if you notice a high evaporation rate.
- Temperature Control: Changes in the temperature of the concrete will impact the curling or contraction, which leads to random transverse or longitudinal cracking. Temperature can be managed by choosing cementitious materials that reduce the rate of hydration and the heat. Avoid using fine cementitious materials. Consider using chilled water or ice to reduce the temperature of the fresh concrete that is used. Additionally, avoid placing the concrete during the hottest times of the day. When the concrete is curing, it is also important to protect the concrete from significant changes in environmental temperatures. The concrete can be insulated using polyethylene sheets or blankets to reduce heat loss from the surface of the concrete.
- Uniform Support: Don’t overlook the importance of uniform support for the prevention of cracks. The base and subgrade need to be carefully prepared before the concrete is placed.
View the complete article here.
Why is maintaining mixture uniformity crucial in concrete projects, and how can one ensure a uniform surface despite variations in materials and environmental factors?
Maintaining mixture uniformity is essential to prevent preventable issues in the final concrete product, and it involves monitoring material properties, adjusting proportions, and conducting various tests for uniformity.
How does workability impact the concrete placement process, and what factors, including environmental conditions and tools, can affect concrete workability?
Workability, determining the ease of laying and compacting concrete, is crucial for successful placement; factors such as water content, aggregates, cement, and environmental conditions significantly influence workability, and changes may indicate variations in other project factors.