
Welding remains a vital joining process in the metalworking industry and it requires in-depth specialist knowledge and skill. Despite the attractive salary, the number of young people taking up this profession continues to decline, as it is often regarded as unappealing, harmful to health, and dirty. This is where cobots come in. Not only do they make welding more interesting and safe, they also make it more profitable—even for small batch sizes.
Today there are several types of cobot (collaborative robot): mobile individual workstations or fully enclosed one or two-station solutions. A diverse range of technical equipment is available, including robot tracks, turn/tilt positioners, automatic extraction systems, and safety doors. High-tech welding machines, processes, and software solutions for offline programming frequently form part of the standard equipment now.
Times have changed and welding is increasingly becoming a high-tech profession. As well as increasing productivity in commercial and industrial enterprises, welding automation will counteract the growing shortage of skilled workers and make the profession cleaner, safer, and more appealing. The career ladder for welders is now high and ranges from a welding specialist to an International Welding Engineer (IWE).
The major advantages of cobot welding systems
Even the best welding professionals can’t produce welds around the clock with a consistent level of quality. Cobots, on the other hand, master this task with ease, and guarantee 100% reproducible, identical welds. Equipped with modern welding machines from Fronius, such as the TPS 400i CMT or the Multiprocess version iWave 400i AC/DC CMT, a wide range of metals can be welded, including steel, stainless steel, aluminum, copper, and titanium. Innovative Welding Packages, such as Low Spatter Control (LSC), Pulse Multi Control (PMC), or the world-famous Cold Metal Transfer (CMT) can also be used.
The LSC function produces a modified, low-spatter dip transfer arc with an increased deposition rate. PMC offers an optimized pulsed arc, with stabilizers for penetration and arc length ensuring the best welding quality and high welding speeds. CMT combines a new type of droplet detachment with a reversing wire motion, whereby the heat input is lower than with a conventional dip transfer arc. This makes the process particularly suitable for thin sheet welding.
“One of the major advantages of cobot welding systems, especially the Fronius systems, is how easy and intuitive it is to program the welding processes. This makes it much easier to get started with automated welding,” emphasizes Christian Neuhofer IWS, Product Manager at Fronius International.
Three steps to the welding program
To program an industrial robot, you need both welding experience and sound programming skills. It’s a completely different story with cobots. With Fronius systems, you simply grab the welding torch, guide it to the starting point, select the right welding torch position, and press the save button on the control handle. Then you set the contour points along the welding sequence to the end point. These points are saved at the touch of a button and form the welding path. Once this has been created, the welding process is programmed—intuitively via drag & drop—using the graphical user interface of the teach pendant.
“Compared to programming industrial robots, cobot teaching requires hardly any training for the majority of applications. Welding specialists in particular, who are used to working with touchscreens and have some computer skills are able to weld their first components after just a few hours,” explains Neuhofer.
Valid welding parameters from your smartphone
Thanks to the practical WeldConnect app, welding specialists have a personal parameter manager at hand at all times. The innovative online welding assistant offers professional support in selecting suitable welding parameters. These can be saved as a job and transferred to the cobot system’s welding machine via NFC signal so welders can get started with welding straight away.
The WeldConnect app can store numerous jobs, which can be accessed at any time. Young welding specialists in particular, who are used to using smartphones, appreciate the app, as it provides reliable welding parameters for a wide range of tasks. Together with the WeldConnect app, cobots are helping to alleviate the shortage of skilled workers and make welding an appealing career choice again.
Mobile and flexible use: the CWC-mobile from Fronius
The mobile cobot system offers an intelligent combination of mobility, advanced welding technology, and outstanding value. It makes it easier for smaller workshops, in particular, to introduce automated welding technology. Thanks to retractable transport rollers, the system is also suitable for welding larger components. “Those who need to weld larger items such as excavator buckets can push the CWC-mobile to the ready-to-weld component with ease,” says Neuhofer, highlighting the versatility of the system.
In addition to its flexibility when welding, the CE-certified cobot system offers no-compromise safety: the power and torque limiter for the articulated arm, mobile welding fume extraction, movable glare shield, and standard-compliant personal protective equipment (PPE)—consisting of puncture-proof gloves, welding helmet, and protective clothing—protect against illness and injuries. This means the CWC-mobile fully meets the requirements of the European Machinery Directive; the precondition for CE certification.
Single and dual systems to suit component dimensions and requirements
With the CWC-S and the CWC-D, Fronius offers two fully enclosed cobot welding cells for one- and two-station operation. Just like the CWC-mobile, both systems feature the latest welding technology.
The CWC-D two-station solution is ideal for welding components with a length of up to 3 meters. If you remove the central partition wall that is screwed to the welding table, this creates an extended work surface of 3,000 x 1,000 x 600 mm for one-station operation.
“With two-station operation, the system enables welding to be carried out in parallel to setup and is ideal for small-series production of components with a maximum side length of 1.5 meters. While welding is being carried out on one side, the other side can be equipped to increase productivity. Both stations can weld components weighing up to 2 tons,” explains Neuhofer.
The smaller, compact CWC-S has been specially developed for components that are no wider than 1.5 meters. Turn and turn/tilt positioners are available for both the CWC-S single system and the CWC-D dual system for circumferential welding of cylindrical components. The turn positioner is optionally available with a tailstock on the longitudinal axis. The Coordinated Motion software option, which is available for all positioners, enables the welding torch and positioner to move in sync. The Robacta Reamer V torch cleaning station is available in the range as an accessory.
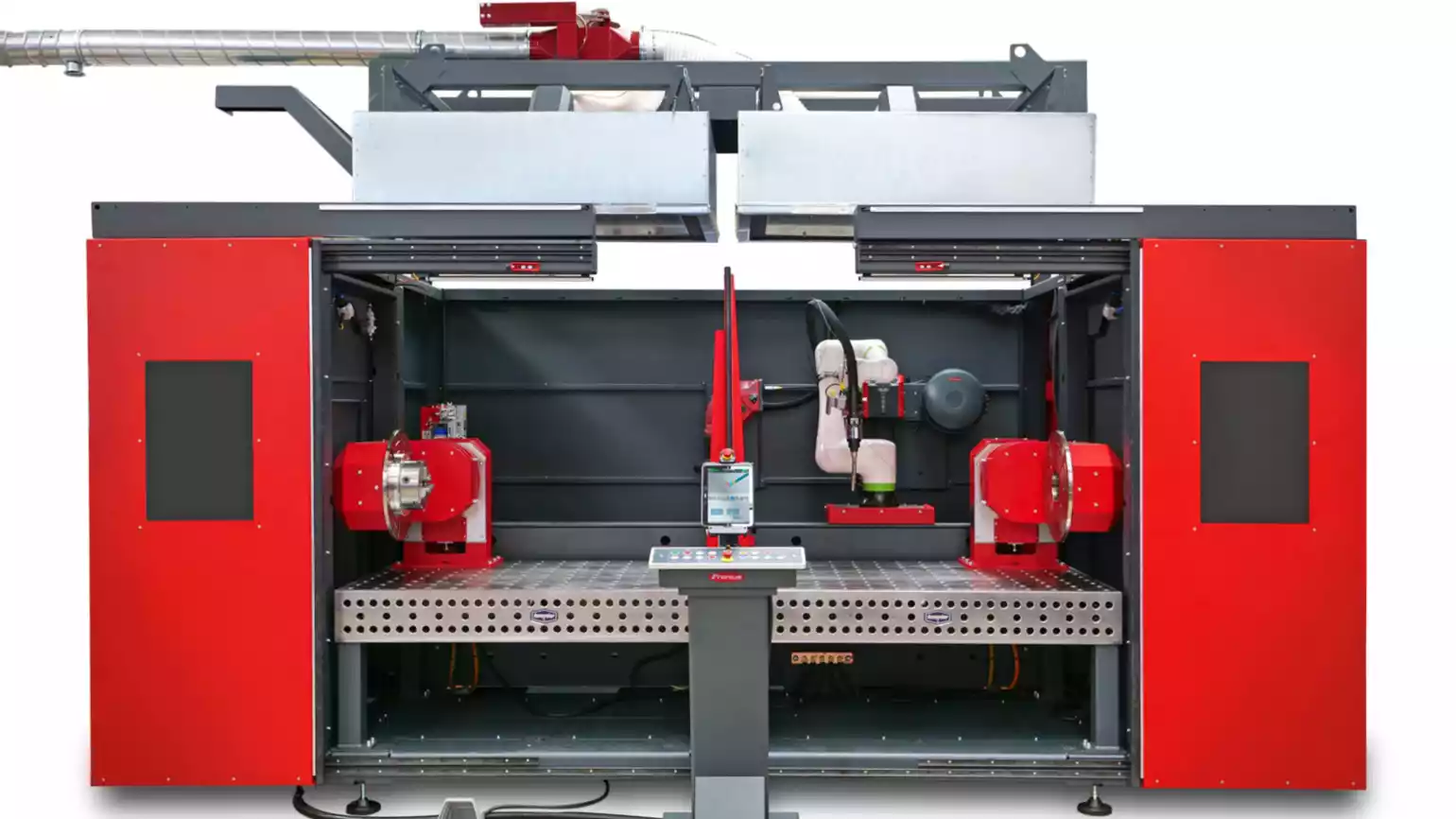
Bringing together cobots and welding robots
The fully enclosed Fronius cobot welding systems CWC-S and CWC-D enable seamless changeover from cobot to robot mode. In this mode, the power/torque monitoring and the speed limiter of 250 mm/s are deactivated, allowing speeds of up to 2 m/s to be reached. If programming is performed with the iPendant robot controller, in addition to high articulated arm speeds, more complex movement sequences can also be carried out and devices can be controlled in robot mode. This allows the full potential of the systems to be unleashed, giving a significant boost to productivity.
Cobots are an ideal way to get started in the world of automation. They enable the robot’s workings to be understood through manual teaching and the kinematics to be learned without a high risk of injury. Welding specialists benefit from better understanding of the kinematic processes, which is an advantage, especially when starting to work with robotic welding later on.
Increase productivity with offline programming
With the Fronius Pathfinder offline programming software, welding processes can be programmed independently of the cobot welding system, without any interruption to ongoing production. Unlike manual teaching, the software enables welds to be copied and mirrored, scanning processes to be created, and complex movement sequences to be simulated. This minimizes downtime and increases productivity by up to 80%, especially for complex component geometries. As soon as a program has been created, it is transferred to the welding cell and manually adjusted if necessary. Another advantage of Fronius is that the software and welding system come from a single source and work perfectly together.
High level of safety with Fronius cobots
Fronius worked with an external safety inspector to carry out a series of intensive safety tests, which delivered impressive results. These tests included attempts to pierce a glove with wire—unsuccessfully! The impact force of the gas nozzle and the edges of the torch holder were also measured and lie safely within the defined limits. Of particular note is the fact that the water-cooled welding torches are lukewarm within seconds, effectively minimizing the risk of burns. All these results confirm that Fronius products meet the highest safety standards and ensure maximum safety.
The path to automation with Fronius
Fronius is there for its customers right from the start and offers customized automation solutions, ranging from simple systems to complex applications.
“As a general contractor, we help our customers select the ideal solutions for them, whether that be cobots, welding robots, or mechanized systems such as welding carriages, circumferential and longitudinal seam welding systems, seam welders, or orbital systems. Our advice doesn’t stop once you’ve made a purchase. We also support our customers during commissioning and have a global service network to provide rapid, reliable help with any problems. This ensures our customers benefit from a high level of efficiency and safety with their welding processes,” concludes Neuhofer.