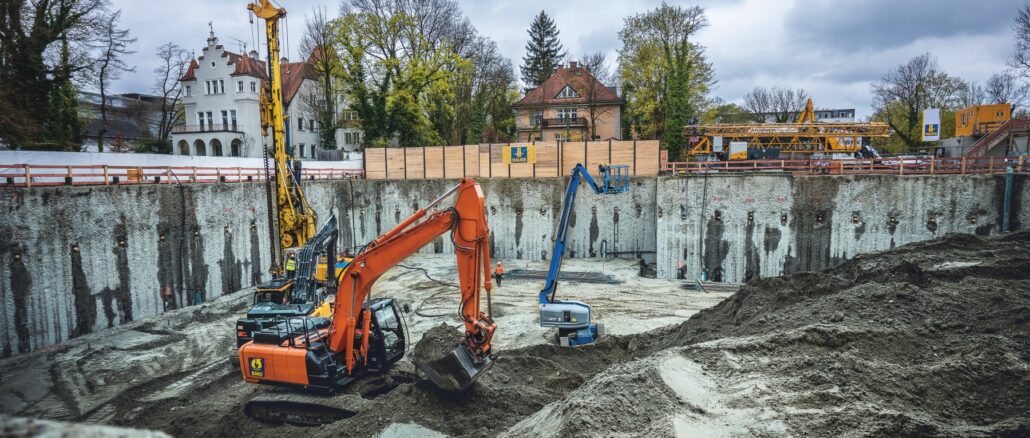
München, Germany – Over an area of 35,000 m2, there was hardly a stone left standing. Most of the buildings on the site in Munich’s Schwabing district were converted or partially demolished in some cases. Only the old wool factory and a garage complex in the northern area of Lodenfrey Park were left as a reminder of old times – but that’s not the case anymore. The former grounds of the textile company Lodenfrey were gradually converted into a modern business park after production was relocated in the 1980s. Now the last remnants of the former textile production factory will also be removed. Where silk, satin, velvet and loden cloths were formerly stored, a modern and groundbreaking new building will soon enrich the campus grounds: Haus K. To make the construction of this new commercial property possible, BAUER Resources GmbH is demonstrating its versatile skill in collaboration with BAUER Spezialtiefbau GmbH, ranging from demolition and pit excavation to foundation engineering and energy.
Demolition without breaking down
The demolition work began in September 2022. But how should this type of industrial construction work be tackled? That’s easy: by relying on experts in the field. Operations Manager Jan Uhlig and Foreman Erwin Resch from the Bauer Umwelt Division of BAUER Resources GmbH are always involved in dismantling projects and provide valuable insider knowledge, for example regarding remnants in the soil and buildings. At this former production site as well, the first step was clearing out and removing contaminated materials – including roofing paper containing asbestos, polluted wood and hazardous insulation material. The subsequent demolition was a piece of cake for the team on site. Using large equipment, the building was gradually dismantled and roughly 35,000 m3 of cubical content were demolished. “Of course, the process was not entirely silent,” explains Machine Operator Bernhard Friedrich from the Bauer Umwelt Division. “But with lots of experience and a sharp intuition, you can also work with a demolition excavator on an urban site with a comparatively low level of noise – that’s something we understand inside-out, along with smooth removal of excavated material.”
Hand in hand to the excavation pit
After the demolition of the building, Jan Uhlig and his team took on the initial excavation of the pit. For the foundation work, they called in their colleagues from Bauer Spezialtiefbau, because the rule is always: Safety first. Since the task was to construct an 8 m deep excavation pit, 3,000 m2 of Mixed-in-Place wall (MIP) were installed. This had to be tied back with roughly 84 anchors and 84 MIP king piles needed to be prepared for geothermal activation. In addition, the Spezialtiefbau team inserted 6 m long GEWI piles into the ground for uplift prevention of the 2,500 m2 foundation slab. At the same time, the Bauer Resources team continued the excavation work on the pit including dewatering. By the end of this joint work, roughly 18,000 m3 of excavated material had been moved and properly disposed of – an enormous effort overall. But thanks to good teamwork, years of experience and close coordination, it was possible to seamlessly interlink the dismantling, excavation and foundation work. “What makes our concept unique: it is a complete solution from a single source. We take care of everything on and below ground all the way to a turnkey excavation pit,” highlights Jan Uhlig. “This offers maximum efficiency and pays off for our customers on the bottom line.”
Geothermal heat as the “green” icing on the cake
Even after the main work was completed, a challenging project phase had to be tackled: geothermal activation of the MIP wall and foundation slab. Like clockwork, the experts from Bauer Resources laid more than 5 km of pipeline on the excavation base for this purpose – a real tough job. Since then, the site has been on pause until the shell and first floor are completed. After that, a thermal response test can be conducted to determine the heat conductivity of the ground, the distributor units can be installed and the geothermal heating and cooling system with an output of roughly 100 kW can be commissioned.