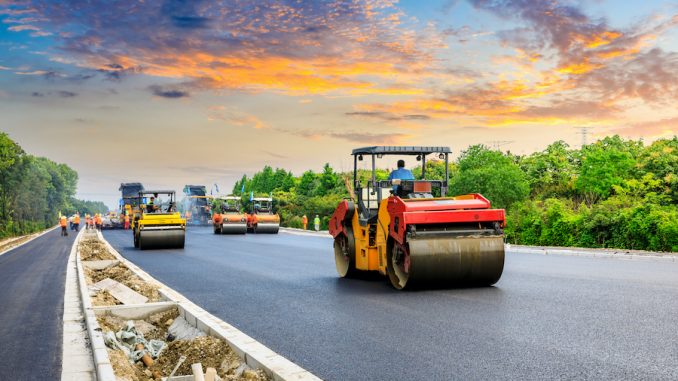
Our Asphalt Design Guide article series, based on the Asphalt Paving Design Guide by Minnesota Asphalt Pavement Association, will give you information about using asphalt in your construction projects. The purpose is to provide a basic knowledge of asphalt pavement design for the interested layperson. It is not intended to take the place of asphalt pavement design done by professional engineers using project specific data.
Asphalt Advantages
The use of asphalt pavement provides a fast, efficient, and economical construction process with unsurpassed versatility. Here we discuss the many advantages to using asphalt.
Durability
Asphalt is a flexible pavement that can withstand occasional over-loads without serious damage. Its resistance to freeze-thaw and de-icing salts provides for superior performance during inclement weather. Its lack of repetitive joints removes the possibility of the blowups that plague Portland Cement Concrete during summer heat waves.
Economical
The Federal Highway Administration has shown that a dollar spent on asphalt pavements goes 26.9 percent further than a dollar spent on concrete pavements. Asphalt is a cost-effective choice because it has a lower first cost than concrete and can be constructed as a perpetual concrete. This results in a lower user cost. Staged construction also helps spread out the cost of placement. Because asphalt pavement has no joints to repair and is not affected by freeze-thaw actions, it is much less expensive to maintain.
Environmental Sustainability
Asphalt is the sustainable material for constructing pavements. From the production of asphalt pavement to the placement on the road, to rehabilitation, through reuse/recycling, asphalt pavements minimize the impact on the environment. Technologies like recycling asphalt pavement, recycling asphalt shingles, warm mix asphalt, porous pavement and other advances help reduce the life cycle costs and environmental impacts of driving surfaces. Asphalt provides a long-life and smooth pavement for users today and for generations to come.
Smoothness
Asphalt pavements will consistently give the driving public the smooth, quiet ride they have come to expect. Since it is machine-placed, it has a uniform surface unsurpassed by other pavements. There are no repetitive joints, noisy surface texture, and blowups with this method of construction, all of which leads to a smoother ride as experienced by the driving public.
Ease of Construction
Since asphalt pavement is machine-placed, there is no need for time-consuming form work and steel reinforcement. After placement, traffic can use the pavement almost immediately – no delay is required to allow it to cure. When repairing roads, an asphalt surface is quicker and easier to complete because there is little down-time waiting for a patch to cure.
Versatility
The versatility and popularity of asphalt pavement is evident across the United States – factories and schools, office parks and playgrounds, and the overwhelming majority of our streets and roads stand as clear testimony that the advantages of asphalt pavement make it America’s first choice for paving and rehabilitation.
Noise
Asphalt pavements are quiet. Data from around the world prove that less traffic noise is generated on asphalt pavement surfaces. Open-graded and Stone Matrix Asphalt (SMA) mixes have been shown to absorb engine and transmission noise.
Recyclable
Another major advantage of asphalt pavement is its ability to be completely recycled. Not only can the aggregates be reused, but the asphalt binder also retains its adhesive properties and can be re-used in a new asphalt pavement mix. Pavements are recycled in a conventional asphalt pavement plant with minimal modifications. Recycled pavements have been tested in the laboratory and in the field and have been proven to perform at least as well as virgin aggregate mixes. Asphalt pavements are 100 percent recyclable; in fact, they are the most recycled product in the United States.
Safety
Asphalt pavements offer high skid resistance values. The dark color of asphalt reduces glare, helps melt ice and snow, and provides a high contrast for lane markings.
Staged Construction
A major advantage for asphalt pavements is the potential for staged construction. The asphalt base course can be placed and used under traffic during initial construction. This base course can then be overlaid with final surface courses. Staged construction improves on-site conditions, removes the aspect of muddy soils, and provides a staging area to store construction materials and equipment. This method also provides an opportunity to discover and correct unanticipated problem areas, such as weak subgrades, poor drainage, or poorly compacted trenches, which can be repaired at a minimal cost prior to final surfacing. The site may also be landscaped prior to placing the wearing course, allowing all construction operations to be finished before the pavement is completed. In so doing, a surfaced parking lot may receive an occupancy permit prior to final placement of the surface, allowing site use sooner, rather than later.
Asphalt Defined
The black cementing agent known as asphalt has been used for road construction for centuries. Although there are natural deposits of asphalt, or rock asphalt, most used today is produced during the refining of crude oil. Asphalt is a constituent of most petroleums and is isolated through the refining process. (See the Petroleum Asphalt Flow Chart below.)
Petroleum Asphalt Flow Chart
Asphalt is called a bituminous material because it contains bitumen, a hydrocarbon material soluble in carbon disulfate. The tar obtained from the destructive distillation of soft coal also contains bitumen. Both petroleum asphalt and coal tar are referred to as bituminous materials. Because their properties differ greatly, petroleum asphalt should not be confused with coal tar. Petroleum asphalt is composed almost entirely of bitumen while the bitumen content in coal tar is relatively low. The two materials should be treated as separate entities.
One of the characteristics and advantages of asphalt as an engineering construction and maintenance material is its versatility. Although a semi-solid at ordinary temperatures, asphalt may be liquefied by applying heat, dissolving it in solvents, or emulsifying it. Asphalt is a strong cement that is readily adhesive and highly waterproof and durable, making it particularly useful in road building. It is also highly resistant to the actions of most acids, alkalis, and salts.
Asphalt Binder
Asphalt is produced in a variety of types and grades ranging from hard-brittle solids to near water- thin liquids. The semi-solid form known as asphalt binder is the basic material used in asphalt pavements. Liquid asphalt is produced when asphalt binder is blended or “cut back” with petroleum distillates or emulsified with water and an emulsifying agent.
At ambient air temperatures, asphalt binder is a black, sticky, highly viscous material. It is a strong and durable binder with excellent adhesive and waterproofing characteristics. Applying heat, which facilitates mixing with mineral aggregates to produce asphalt pavement, can readily liquefy asphalt binders.
The largest use of asphalt binder is for asphalt pavement. After compacting and cooling to air temperature, asphalt pavement is a very strong paving material with the ability to sustain heavy traffic loads while remaining flexible enough to withstand ambient environmental conditions and stresses. Over 96 percent of the hard-surfaced roads in the United States are paved using asphalt pavement.
Emulsified Asphalts
Emulsified asphalts (also known as emulsions) are low-viscosity mixtures of tiny asphalt binder droplets, water, and emulsifying agents. The emulsifying agent coats the surfaces of the asphalt droplets and keeps them suspended in the water prior to application. After application, the asphalt emulsion breaks, and the water separates and evaporates. Emulsions are brownish in color during application, but after breaking, the asphalt binder returns to its original black color.
Emulsions are used for a Tack Coat between subsequent layers of asphalt pavement to aid in binding the layers together.
Cut-Back Asphalts
Cut-back asphalts are low-viscosity liquid asphalt mixtures manufactured by diluting (cutting back) Asphalt Binders with petroleum solvents (cutter stock or diluent). After application, the petroleum solvent evaporates, leaving the asphalt binder residue.
Cut-Back asphalts may be used as a tack coat between subsequent layers of asphalt pavement, particularly when ambient air temperatures are cool.
Asphalt Binder Grading
Asphalt binders appropriate for pavement construction were previously graded based on resistance to penetration and/or viscosity measures. Currently, asphalt binders are graded based on the temperature range over which the binder retains certain desirable characteristics. These desirable characteristics include adequate flexibility to resist cold temperature cracking and sufficient rigidity to resist warm temperature rutting. The current grading system is known as the Performance Grading (PG) system
Performance Grading
Performance grading specifications were developed as part of the Strategic Highway Research Program (SHRP) and are a major component of SUPERPAVE. Binders are specified on the basis of the climate and pavement temperatures in which the binder is expected to serve. For example, performance graded (PG) binders used in Minnesota vary from north to south and with intended use; however, PG 58-28 is the most commonly used grade. The first number (58) represents the average 7-day maximum pavement design temperature in degrees Celsius. This maximum temperature establishes the upper temperature limit for the binder to retain adequate rigidity to resist rutting.
The second number (-28) represents the minimum pavement design temperature in degrees Celsius. The minimum temperature establishes the lower limit for the binder to retain sufficient flexibility to resist thermal cracking.
Physical properties of the binders are measured at various temperatures both before and after laboratory aging. The laboratory aging is conducted to simulate field conditions imposed during the asphalt pavement production process as well as from long-term environmental exposure. Binder physical properties are typically measured using four devices:
- Dynamic Shear Rheometer
- Rotational Viscometer”
- Bending Beam Rheometer
- Direct Tension Tester
Aggregates
Aggregates (or mineral aggregates) are hard, inert materials such as sand, gravel, crushed rock, slag, or rock dust. Properly selected and graded aggregates are mixed with the asphalt binder to form asphalt pavements. Aggregates are the principal load-supporting components of an asphalt pavement, totaling approximately 95 percent of the mixture by weight.
Classifications
Paving aggregates are classified according to source or means of preparation. A brief description of the classifications follows:
Pit or Bank-Run Aggregates
Gravel and sand are pit or bank-run natural aggregates. They are typically screened to proper size before being used for asphalt paving purposes.
Processed Aggregates
When natural pit or bank-run aggregate has been crushed and screened to make it suitable for asphalt pavements, it is considered a processed aggregate. Crushing typically improves the particle shape by making rounded particles more angular.
Crushed rock is also a processed aggregate. It is created when the fragments of bedrock and large stones are crushed so that all particle faces are fractured. Variation in size of particles is achieved by screening.
In the processing of crushed rock, the fines produced are separated from the other crushed aggregate and may be used as manufactured sand in asphalt pavements.
Synthetic Aggregates
Aggregates produced by altering both physical and chemical properties of a parent material are called synthetic or artificial aggregates. Some are produced and processed specifically for use as aggregates; others are the byproduct of manufacturing and a final burning process. Blast furnace slag is an example of a synthetic aggregate.
Desirable Properties of Aggregates
Selection of an aggregate material for use in an asphalt pavement depends on the availability, cost, and quality of the material, as well as the type of construction for which it is intended. To determine if an aggregate material is suitable for use in asphalt construction, it should be evaluated in terms of the following properties.
Size and grading. The maximum size of an aggregate is the smallest sieve through which 100 percent of the material will pass. The Nominal Maximum size is the next sieve larger than the sieve on which 10 percent of the material is retained. How the asphalt pavement mixture is to be used determines not only the appropriate maximum aggregate size, but also the desired gradation (distribution of sizes smaller than the maximum).
Cleanliness. An excess of foreign or deleterious substances such as shale, oxides, unsound cherts, and/or organic material make some materials unsuitable for paving mixtures.
Toughness. Toughness or hardness is the ability of the aggregate to resist crushing or disintegration during mixing, placing, compacting, and other procedures associated with construction or traffic loading.
Soundness. Although similar to toughness, soundness is the aggregate’s ability to resist deterioration caused by the weather. For example, the stresses placed on materials during freezing and thawing.
Particle shape. The shapes of aggregate particles influence the asphalt mixture’s overall strength and workability as well as the density achieved during compaction. When compacted, irregular particles such as crushed rock tend to lock together and resist displacement.
Absorption. The porosity of an aggregate permits it to absorb asphalt and form a bond between the particle and the asphalt. A degree of porosity is desired, but aggregates that are highly absorbent are generally not used. Absorption is a significant factor in asphalt pavement mix design.
Stripping. When the asphalt film separates from the aggregate because of the action of water, it is called stripping. Aggregates coated with too much dust also can cause poor bonding, which results in stripping. Aggregates readily susceptible to stripping action usually are not suitable for asphalt paving mixes unless an anti-stripping agent is used.
The attributes mentioned above are quantitatively measured by standard physical tests and limits are included in standard materials specifications.
Asphalt Pavement
Asphalt pavement is known by many different names: asphalt pavement, asphaltic concrete, plant mix, bituminous mix, bituminous concrete, hot-mix asphalt, warm-mix asphalt, and many others. It is a combination of two primary ingredients – aggregates and asphalt binder. The aggregates total approximately 95 percent of the total mixture by weight. They are mixed with approximately 5 percent asphalt binder to produce asphalt pavement.
The aggregates and asphalt are combined in a manufacturing plant capable of producing specified materials. Plant equipment includes: cold bins for storage and controlled proportioning of graded aggregate; a dryer for drying and heating aggregates to the required mixing temperature; a pug mill or drum for combining the graded, heated aggregate and liquid asphalt cement according to specified mix formulas, and tanks for storing the heated liquid asphalt.
Asphalt pavement is transported by truck to the paving site where it is spread to a uniform thickness with a mechanical paving or finishing machine. The material is then compacted to the required degree by heavy, self-propelled rollers, producing a smooth pavement course.
The paving or finishing machine places the asphalt pavement at temperatures between approximately 225° and 300° F., depending on the mixture characteristics, layer thickness, and ambient conditions. The material should be compacted before the mix temperature falls below optimum compaction temperature, dependent on ambient conditions, to achieve adequate density.
Conclusion
Covering more than 96 percent of the nation’s paved highways, asphalt pavement is the most widely used paving material in the United States. For versatility, durability, and ease of construction, it has no equal. In the next article in the Asphalt Paving Design series we discuss design considerations such as traffic, soil support capability, and pavement thickness.
What are the advantages of using asphalt for construction projects?
Asphalt offers durability, cost-effectiveness, environmental sustainability, smoothness, ease of construction, versatility, noise reduction, recyclability, high skid resistance, and the potential for staged construction.
How is asphalt defined, and what are the key components of asphalt pavement?
Asphalt, derived from crude oil refining, is a bituminous material serving as a strong cement in road construction, with key components including asphalt binder, emulsified asphalts, cut-back asphalts, and aggregates.