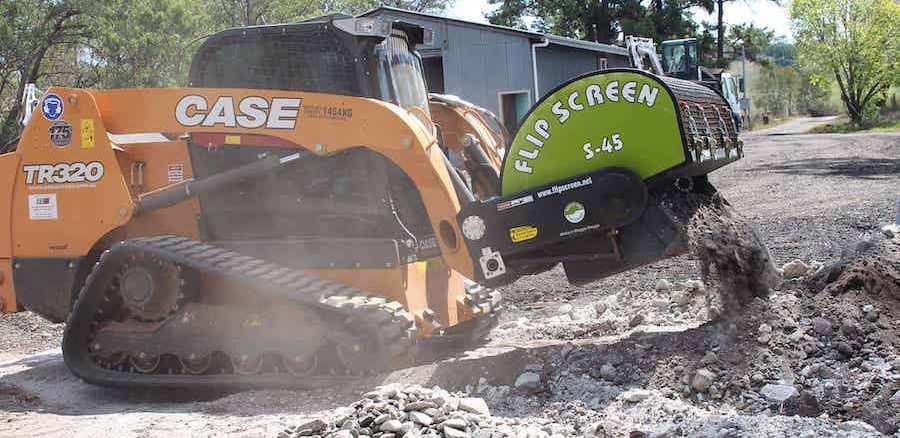
The Flipscreen is a high volume, patented, screening bucket that inexpensively and efficiently screens any material, on-site, for any industry. It is Australian Made and owned.
Limitless in terms of material, the specially designed shape of the bucket provides seamless screening, with no moving parts in the bucket that can break down or get clogged up, like so many others. This means that if you can scoop it up, you can screen it. It also means far fewer maintenance and breakdown concerns.
From Corrosive materials to scrap metal to digging the fresh ground and working underwater, the Flipscreen does it all.
Made to suit any size excavator, Loader, skid steer, or tractor with zero daily maintenance on new direct-drive models.
FlipScreens are replacing trommels and screening plants as they screen more, at greater profits, are a portion of the cost, and have lower operating expenses. One carrier machine combined with a Flispcreen in a quarry and you are operational!
Grizzly screens become obsolete when faced with an attachment that handles the material once and saves on time. Take the screener directly to the product, not the product to the screener.
FlipScreen is truly portable, reduces hauling and labour costs, and can be changed between carriers very easily or even floated on a carrier between sites.
All industries requiring a primary separation process benefit.
From large mines to local landscape businesses, FlipScreen has reinvigorated the way sites are operated.
We have a Flipscreen to suit any size carrier, here is a list of videos with examples per carrier type, showing sizes in descending order.
Skid Steer Bucket Sizes:
Loader Bucket Sizes:
Excavator Bucket Sizes:
And don’t forget that a Flipscreen can also fit onto any Tractor, backhoe, or telehandler, as seen in this video:
Let’s have a look at more of the features which make us so unique:
Changeable Screens
Screens range in size from 6mm to 300mm, with customs sizes made as well. Screens are also changed on-site, in under 5 minutes, with one operator and no tools.
Largest Screening Area
Compared to other attachments on the market, FlipScreen has the largest screening surface area of its class.
Take the total square feet of a Flipscreen mesh and do the math.
24 rpm is the rotation speed of the WL280 Flipscreen. The WL280 mesh is 110 square feet = 8′ X 12′. How many screening plants do you know with a 12 x 8-foot screen deck?
Not many, that’s right.
We are talking about the biggest fixed plant screen decks.
So at 24 RPM, the Flipscreen puts the material over the mesh every 2.4 seconds (60/25=2.4).
It not only puts the material over this mesh every 2.4 seconds, but it also inverts it, or as we call it “Flips” the material which no other screener does. The WL280 is capable of screening 387yd³ per hour with cycles every 26 seconds.
Direct Drive
Our direct drive models have the final drive motor attached directly to the screening bucket, eliminating chains, sprockets, and internal moving parts.
- It is quieter to operate with non-stick hard-wearing internal hopper liners and hydraulic cylinder actuated ratchets.
- Bolt-on hitch.
- More powerful drives are capable of 23200 Nm versus 9750Nm in current machines.
- Direct drive creates even smoother action.
- Integrated braking system.
- More steel where it is needed and less where it is not.
- No service or greasing daily
- Service period is 1500 hours (oil change in the final drive).
- No chains to service.
- Stainless steel bearings requiring no service.
- The machine is lighter.
- The hitch is closer to the cutting edge, making it more compact to operate.
Smart Valve
Allows for any hydraulic flow and pressure without modification of the carrier.
This has been designed by Flipscreen’s R&D team. And is a revolution in hydraulic attachments. Invented by Flipscreen Australia, July 2012.
Mixing Screen
Our compact Plate Mixer top is a solid screen with internal agitator paddles that allows materials to be mixed.
The mixer removes the need for multiple attachments and equipment. Just roll the mesh off the bucket and roll the mixer plate on.
The mixer top can also be used for: – Dry Mix – Wet Mix – Fertiliser – Sand – Top Soil – Batching, etc. The mixer removes the need for multiple attachments and equipment.
Brush Kit
Rolls with mesh on every rotation maximising productivity.
Our Brush Kit opens the apertures on the mesh on every rotation, preventing the build-up of material and ensuring even screening of material.
So now that you know a little more about the design features of the Flispcreen, if you have any other questions, click here to view more information.
How quickly can I change FlipScreen's screens, and is it a complicated process?
Screens can be changed on-site in under 5 minutes by a single operator with no tools required.
What is the advantage of FlipScreen's Smart Valve, and how does it revolutionize hydraulic attachments?
FlipScreen's Smart Valve allows for any hydraulic flow and pressure without modification of the carrier, providing a versatile and revolutionary hydraulic attachment design.